Bei meinem Truck wurde auf Wunsch des Patienten die Ladepritsche durch Kippergelenke ersetzt. Damit ruht die Wohnbox nicht mehr auf einer Ladefläche, sondern ist direkt mit dem Leiterrahmen des LKW verbunden. Prinzipiell eine super Sache, denn so spart man beim DAF T244 rund 800 kg ein. Das drückt den Truck, der als 10-Tonner konzipiert wurde, garantiert auf unter 7,5 Tonnen. Reisefertig.
Das Ganze sollte natürlich von einer Firma gemacht werden, die sich mit solchen Arbeiten auskennt. Und für die Begriffe wie Verschränkung, Lagerung der Kabine oder Verwindung des Rahmens keine Fremdbegriffe sind. Ich hab da mehr oder weniger blind der Firma Fischer Fahrzeugbau aus Kirchheimbolanden vertraut. Relativ schnell haben sich mit dem Entwurf unterwegs Probleme ergeben.
Zunächst ist mir die Kabine hinten abgerissen, weil sie nur an ein paar Nieten hing. Dann ist die Kabine vorne aus der Lagerung gesprungen. Es ist nicht übertrieben wenn ich sage, dass mit diesem Murks mehrmals lebensgefährliche Situationen geschaffen wurden.
Die ganze Geschichte (Teil 1 Kippergelenke) ist hier: Umbau vom DAF T244 Truck auf Kippergelenke
Immer wenn man denkt: jetzt kann nichts Schlimmes mehr passieren – oder – schlimmer kann es gar nicht mehr werden … passiert: GENAU DAS.
So war ich in Sardinien etwas verwundert über zwei neu entstandene Löcher in dem Kippergelenk.
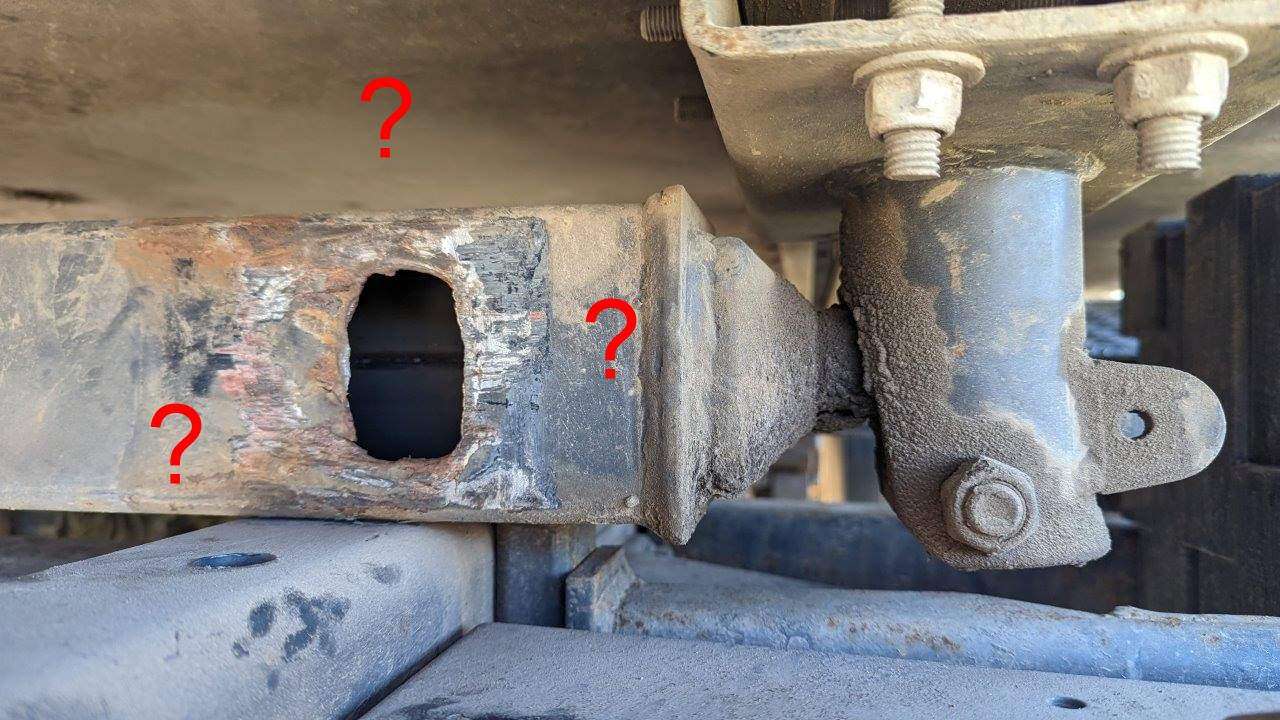
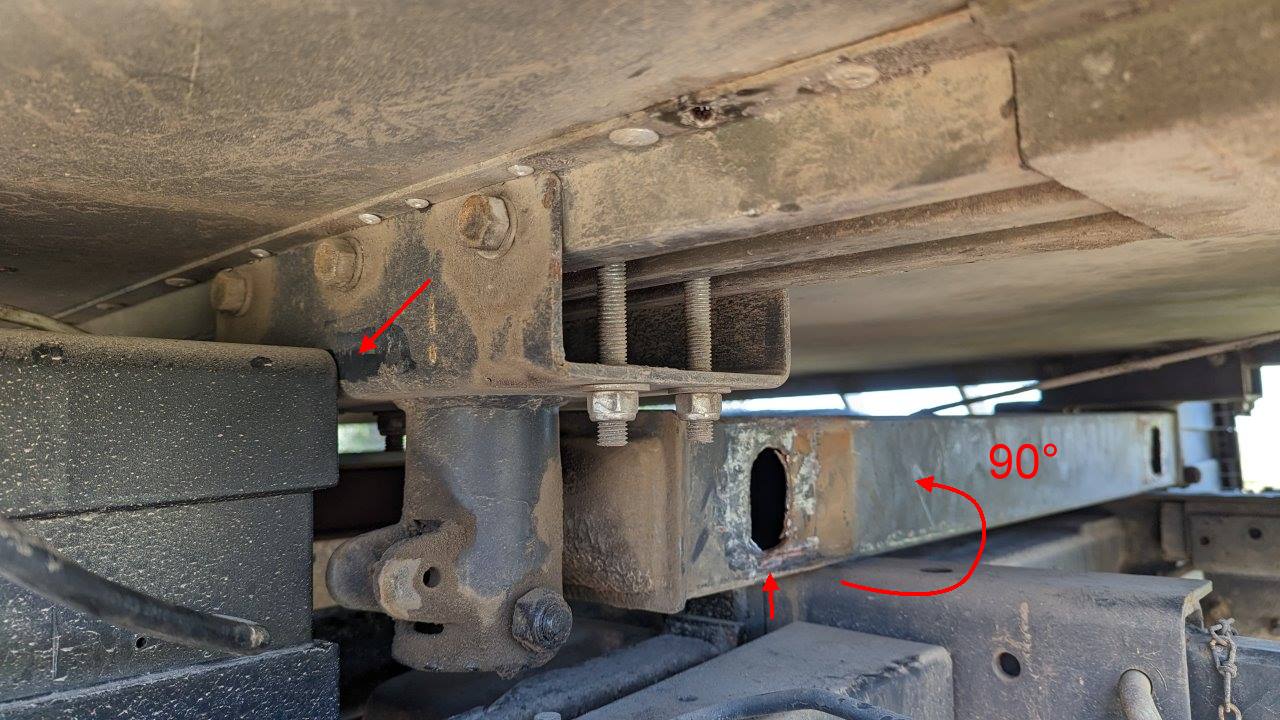
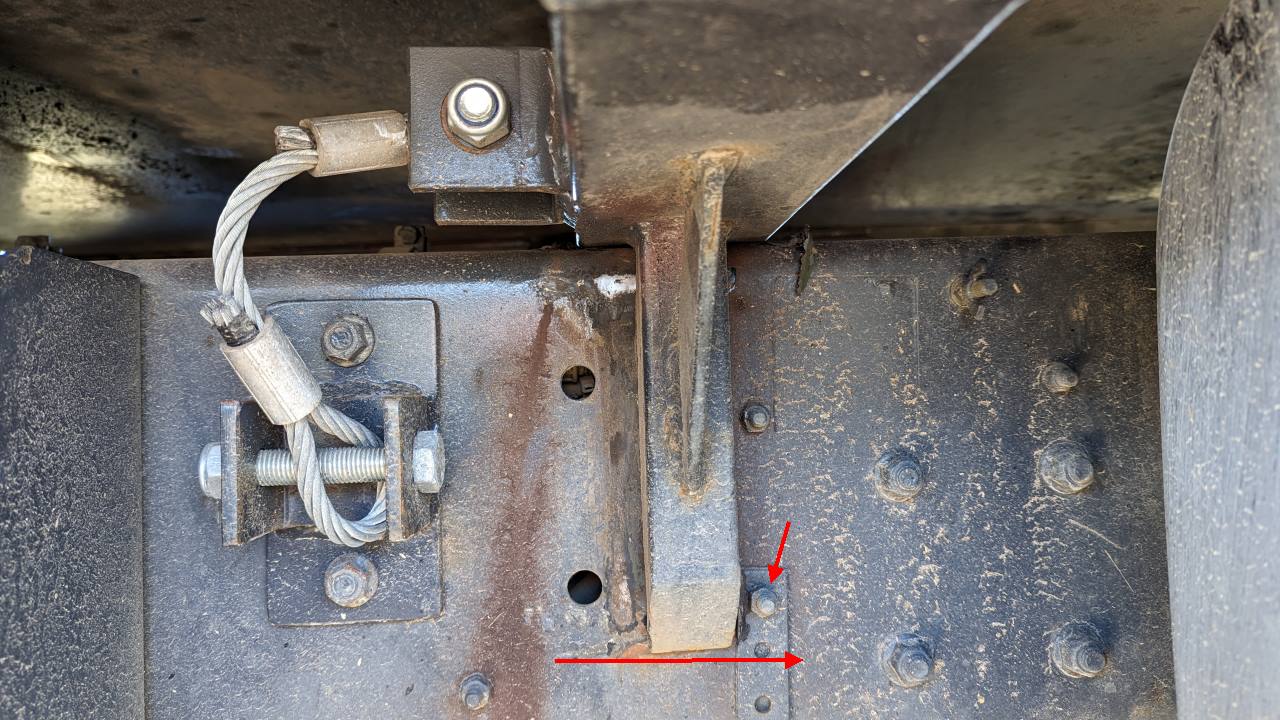
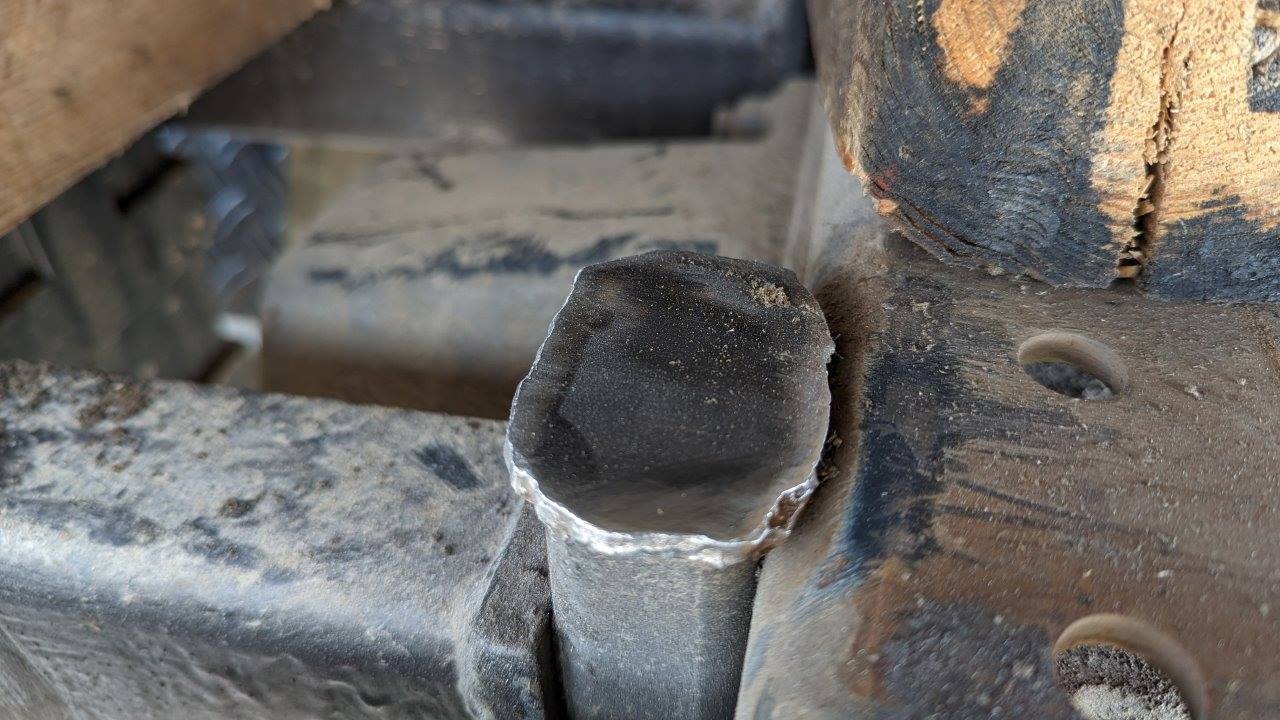
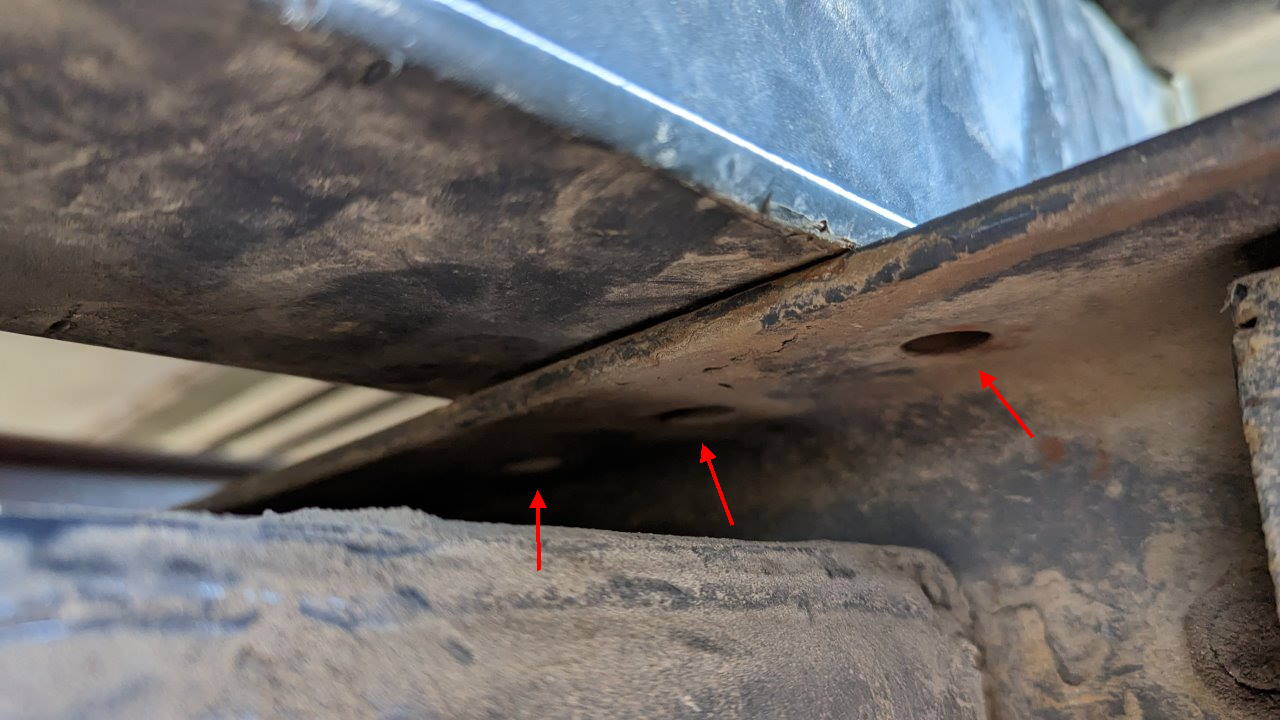
Was für ein lebensgefährlicher Pfusch. Die gesamte Kabine hängt an zwei Schweissnähten mit ca 12 Zentimeter Länge und zwei Schrauben pro Seite. Das konnte ja nicht gut gehen.
Die erste Rettungsaktion / Notreparatur
Nun musste sofort was passieren, direkt dort auf dem Parkplatz am Meer. Ich hab dann Axel angerufen, den ich in Fordongianus kennen gelernt hab. Zum Glück war er noch auf der Insel und hatte Zeit. Und Bock auf die Aktion.
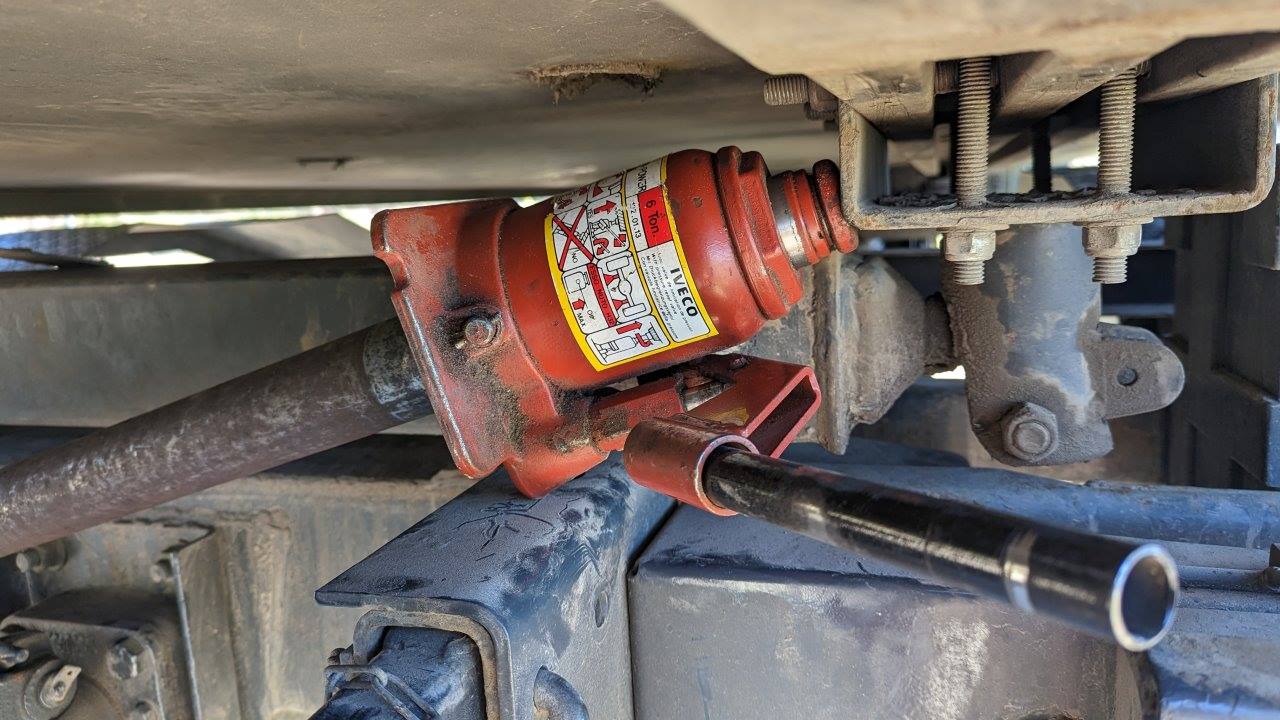
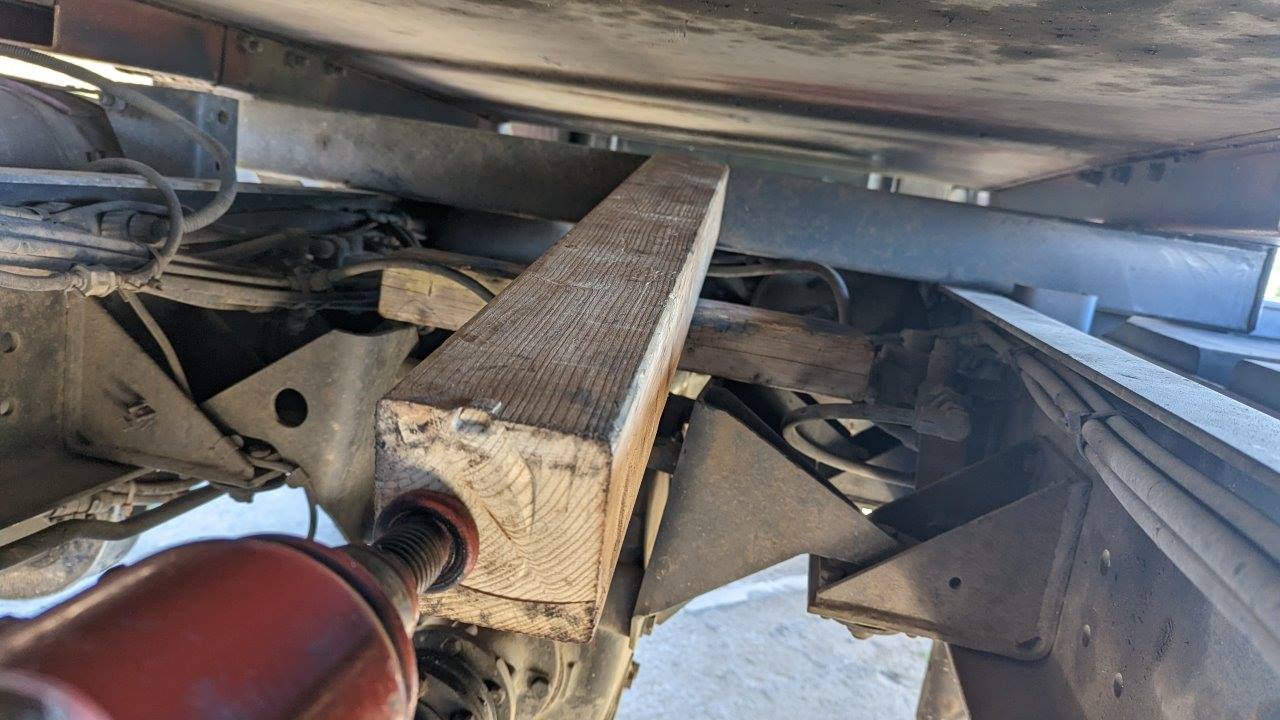
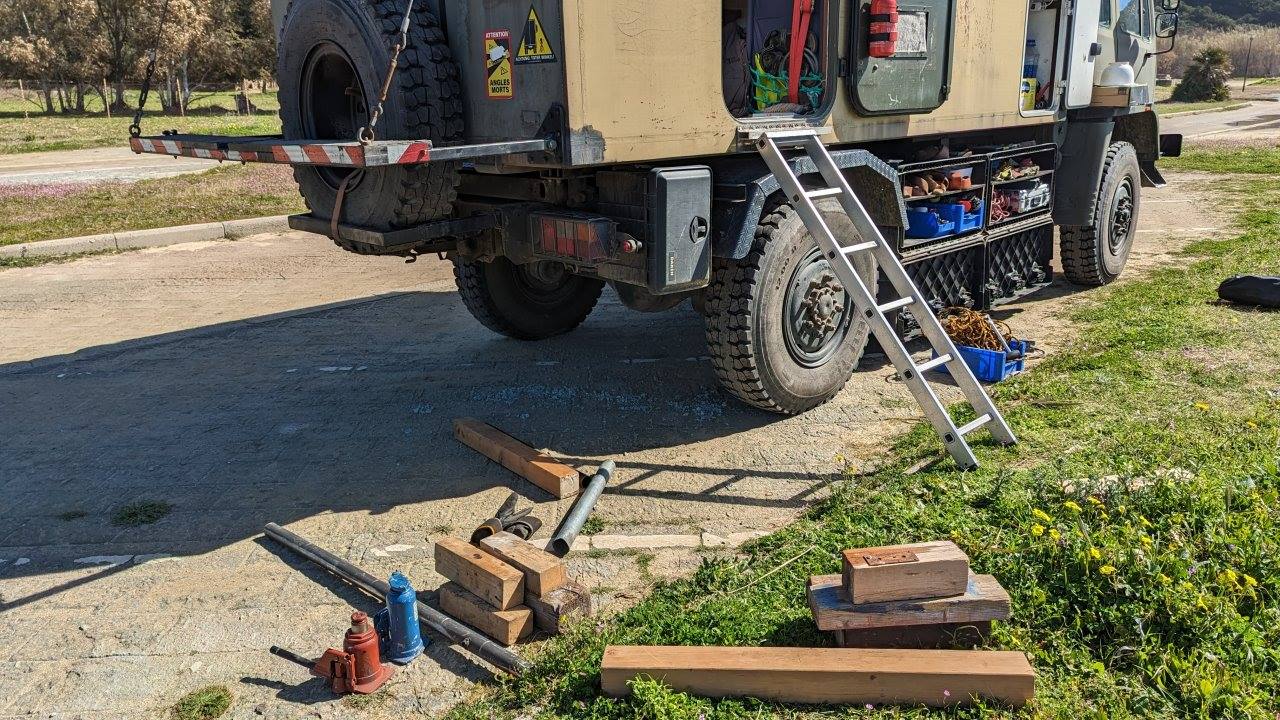
Balken und Klötze aus Holz sind in so einer Situation absolut unverzichtbar. Um Druck aufzubauen, aber auch zum unterlegen. Um alles zu sichern.
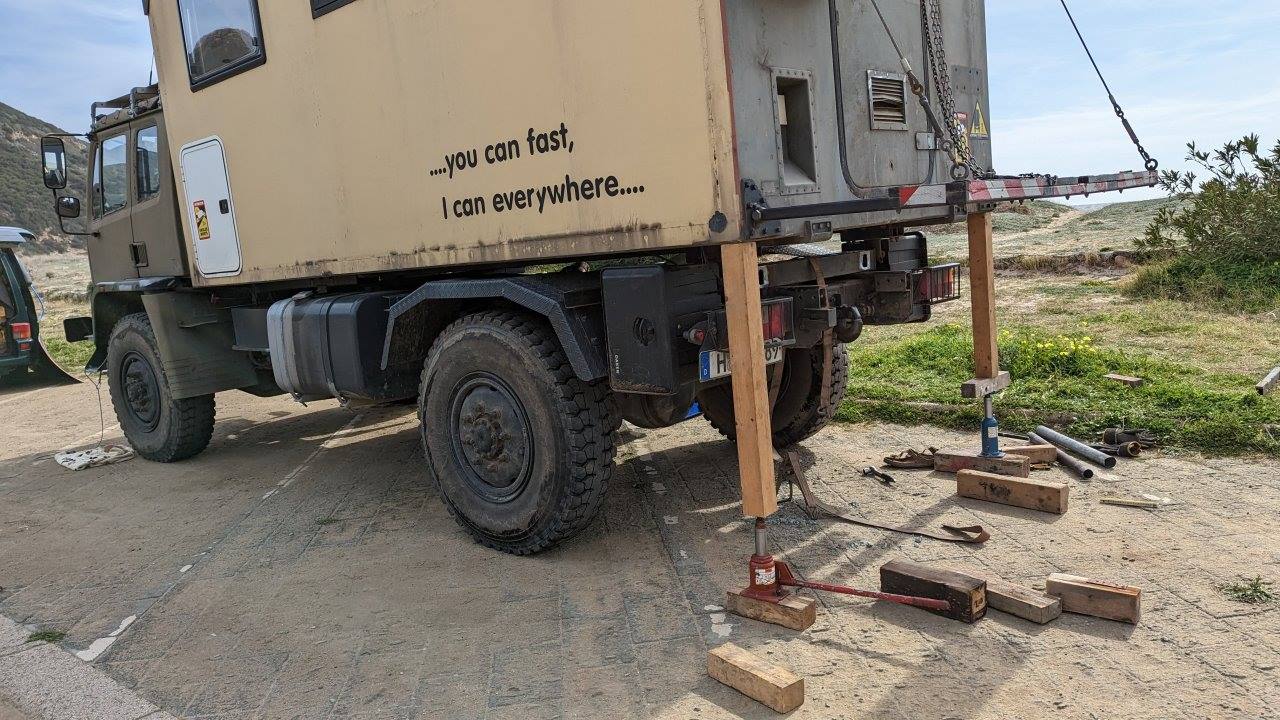
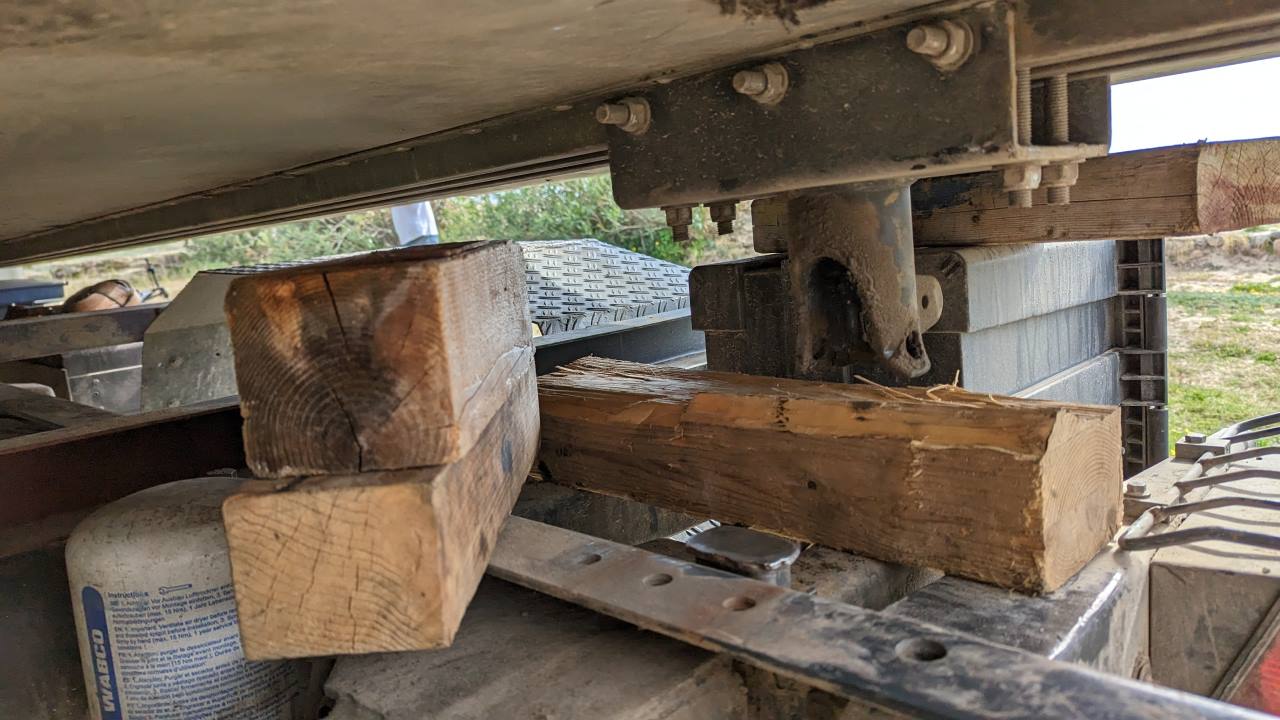
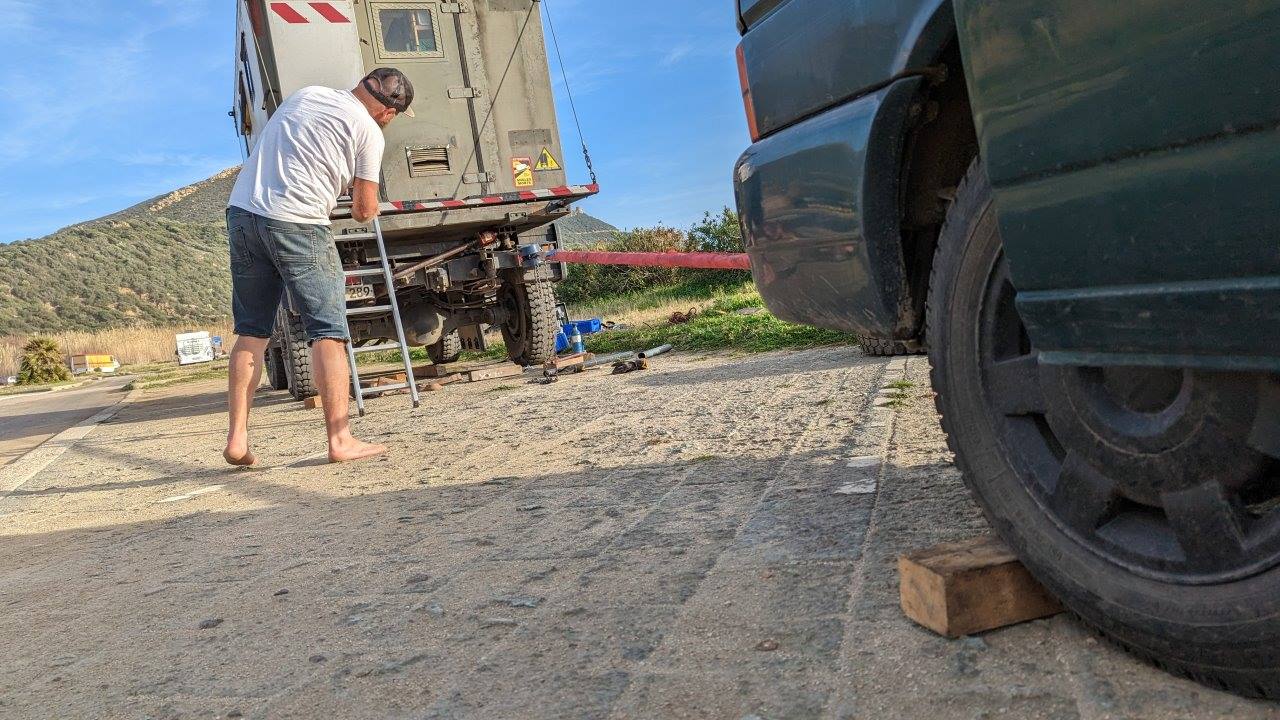
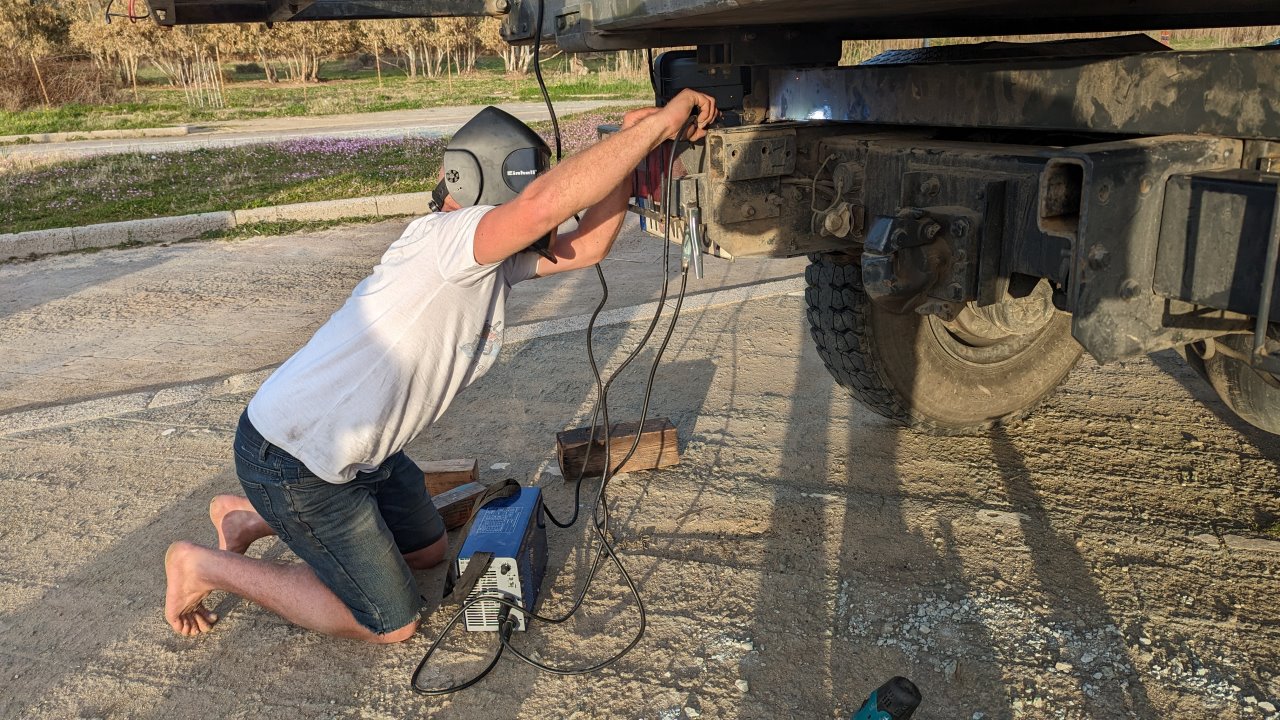
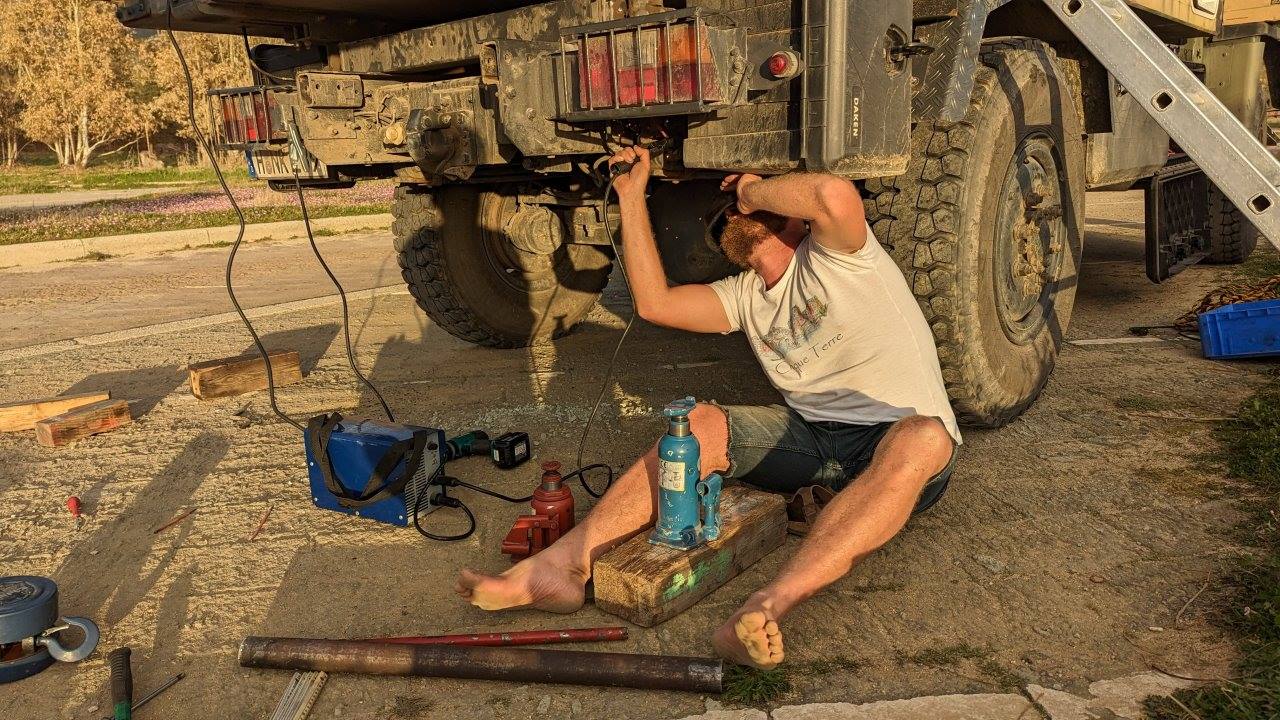
Ich hab tatsächlich ein Schweissgerät an Board. Natürlich noch nie verwendet, Elektroden alle noch original verpackt. Okay, wer ist verrückt genug, ein Schweissgerät durch die Gegen zu kutschieren ? Aber wie man sieht, braucht man alles irgendwann einmal.
Was ich tatsächlich nicht wusste war, ob ich das Schweissgerät überhaupt mit meiner 230 Volt Anlage einsetzen kann. Antwort: gerade so. Bei dem Victron Multiplus 3000 VA ging zwar ständig die Overload LED an, aber sowohl Schweissgerät als auch der Wandler haben es gepackt.
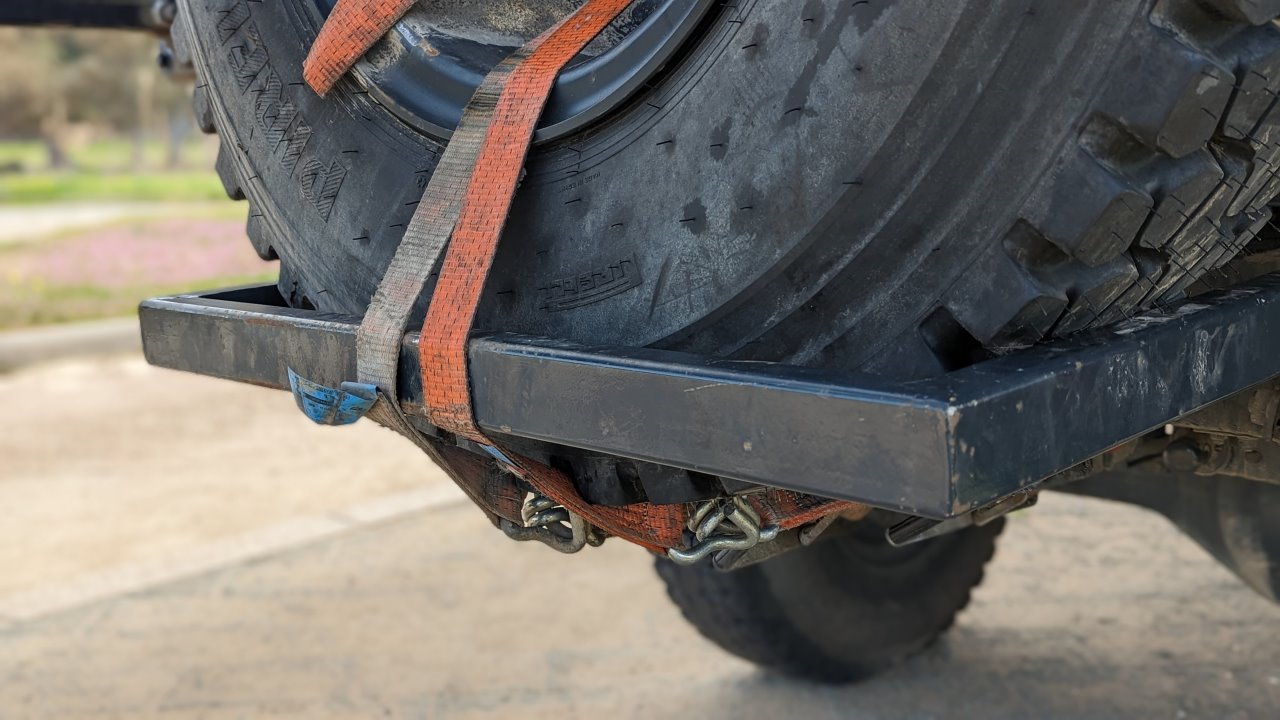
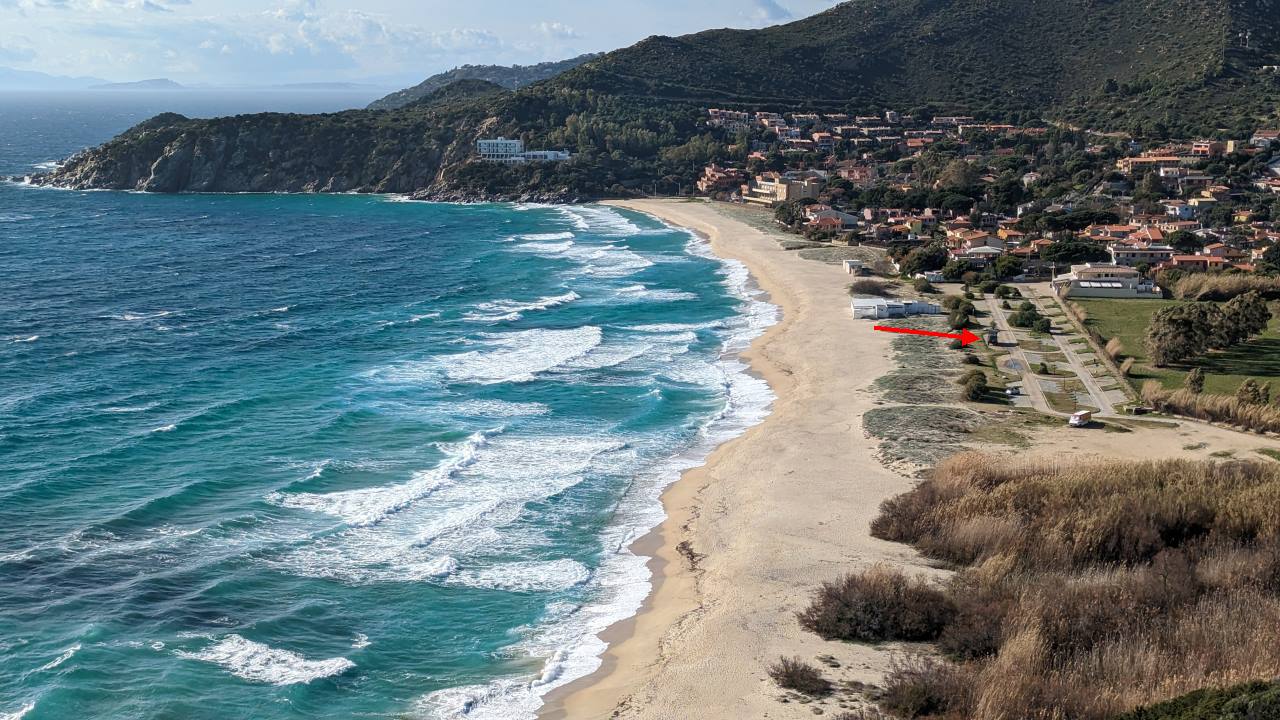
Eine erste, stabile Reparatur unter Feldbedingungen in Sardinien
Eigentlich bin ich ex-Radio und Fernsehtechniker / ex-online Händler und kaum qualifiziert, etwas über Karosserie oder Fahrzeugbau zu schreiben.
Aber dass man eine zwei Tonnen schwere Kabine nicht einfach nur am LKW festnieten sollte hatte ich inzwischen auf die harte Tour rausbekommen. Und vier Schrauben an zwei Halterungen, die man eher beim einem Veranda Tisch wiederentdecken würde – war ebenfalls zu wenig.
If you want something done, do it yourself. (Wenn du etwas erledigt haben willst, tue es selbst)
Gary Oldman als Boss von Zorg Industries im Film „Das Fünfte Element“. Als er gezwungen ist wegen gewisser Misserfolge seiner Handlanger die von ihm selbst gelegte Bombe wieder zu entschärfen.
Doch zunächst musste etwas Material eingekauft werden. Ich hab als erstes einen Holzladen geplündert, um an noch mehr dicke Balken zu gelangen. Dann brauchten wir Metall Profile und Gewindestangen.
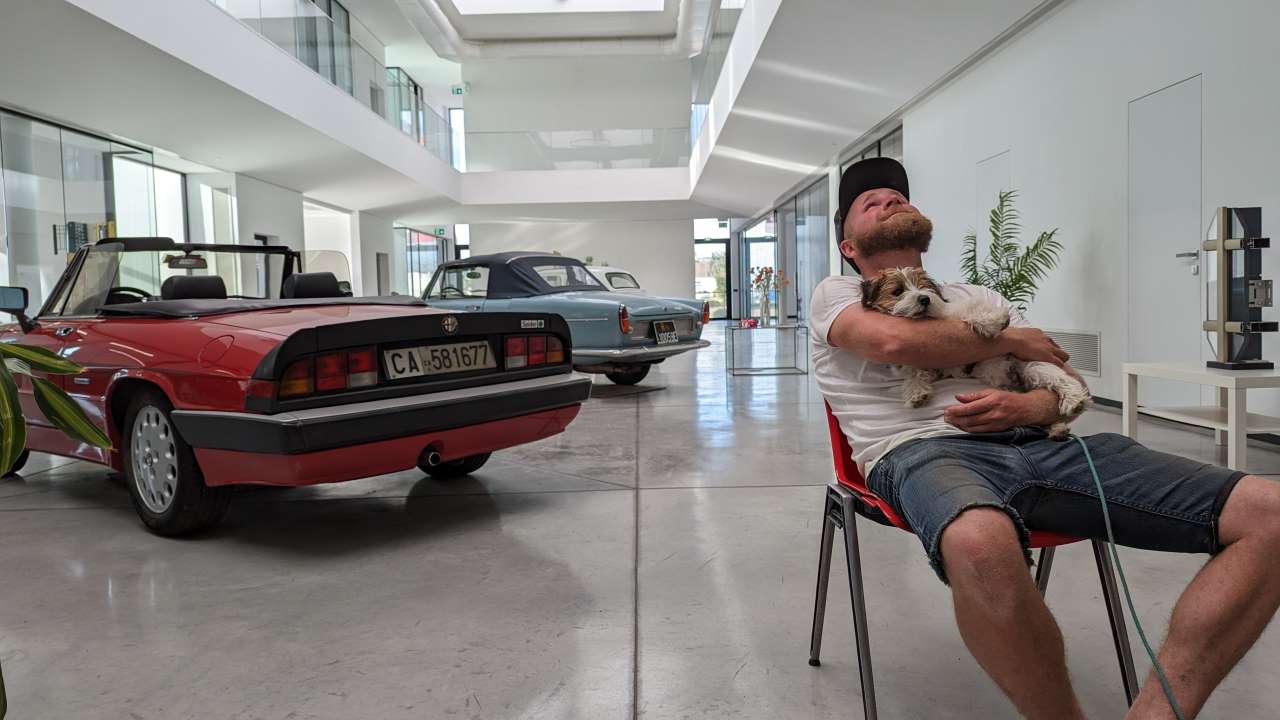
Axel kann ein bisschen Italienisch, ich gar nicht. Es war ein lustiges Unterfangen, dort die richtigen Materialien zu besorgen. Denn Englisch können die Italiener nur in den seltensten Fällen und uns fehlten die Fachbegriffe. Den gewünschten 80 x 40 Vierkant in 5 mm gab es, aber: Mindestabnahme 6 Meter …
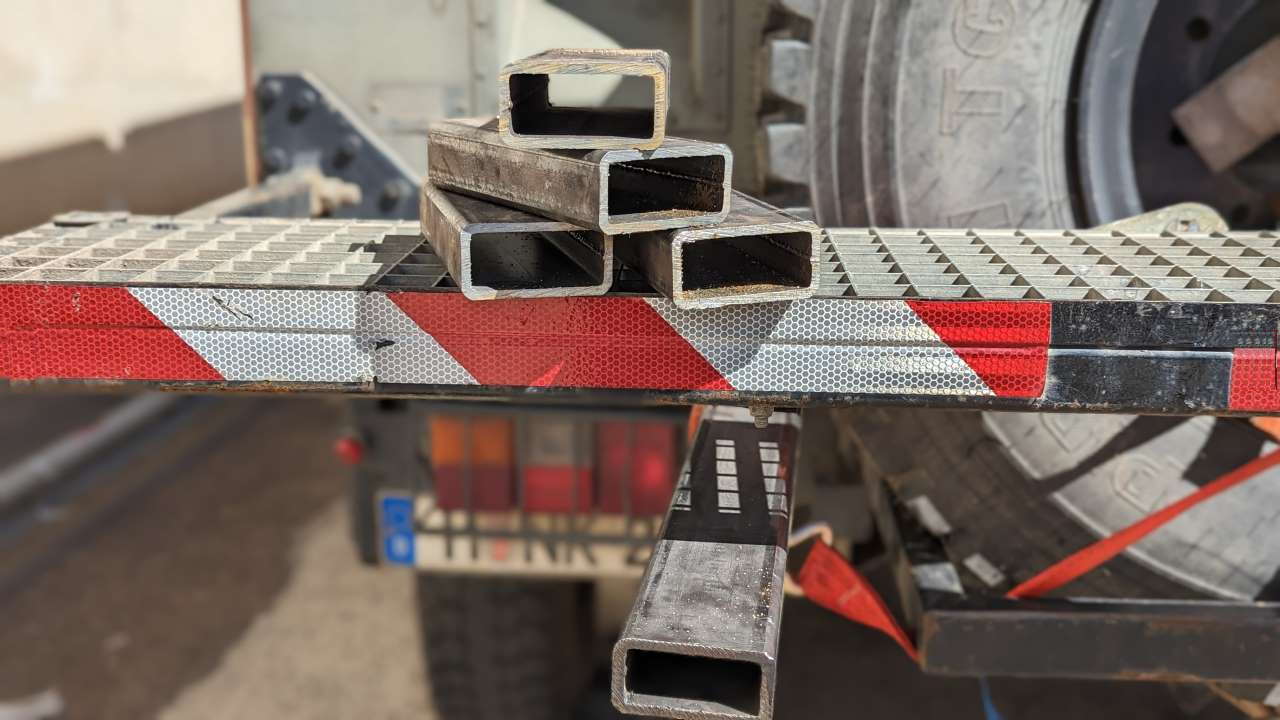
Tja davon brauchten wir eigentlich nur 2x 20 cm. Ich hab mir dann vier Stücke mit 20 cm abschneiden lassen und den Rest von 5,20 Metern unterm LKW verstaut. Und das ganze ohne mit der Wimper zu zucken bezahlt. Ging ja nicht anders. Axel: fassungslos.
Gewindestangen und Muttern brauchen wir auch noch. Ich, das Handy mit der Abbildung einer Schraubenmuttern hochzeigend: „davon eine Packung“. Der Verkäufer: „gibt es nur einzeln. Wie viele brauchst du ?“
Die Mindestabnahmemenge für Flachstahl ist daher 6 Meter, was sich kaum mit einem Fiat 500 wegschleppen lässt. Dafür kann man bei Marini eine einzelne M4 Mutter kaufen und der Verkäufer macht dafür einen Auftrag und druckt es aus. Komische Firmenpolitik, aber egal, wir hatten, was wir brauchten. Darüber war es Feierabend geworden. Wir hatten viel gelacht, neue italienische Wörter gelernt, den Laden aufgehalten und Google Translate strapaziert.
Koordinaten von Marini: 39.29924,9.061629 (SS131 westlich von Sestu)
Nun brauchen wir einen Platz zum werkeln.
Glücksfall war an der Stelle Chelu Noleggio Camper (Webseite) mit dem ich sehr gute Erfahrung gemacht hab. Die Firma ist eher ein Vermieter für Campingfahrzeuge. Der Besitzer hat viele Pläne und vergibt durchaus auch Übernachtungsplätze. Aktuell ist die Firma jedoch eher als Parkplatz und Versorgungsstation zu sehen und nicht als Campingplatz. Der Besitzer ist total nett, spricht perfekt Englisch und hatte keine Einwände, auf seinem Parkplatz vorübergehend eine Open Air Karosserie Reparaturwerkstatt zu eröffnen.
Es gab: Platz ohne Ende, Wasser, Abwasser, satte 16A Strom für das Schweissgerät. Perfekt für uns.
Koordinaten: 39.23338,9.21972 (Am Ostende und letzten Kreisel vom Poetto Strand, Ecke Viale Europa und Via Fiume)
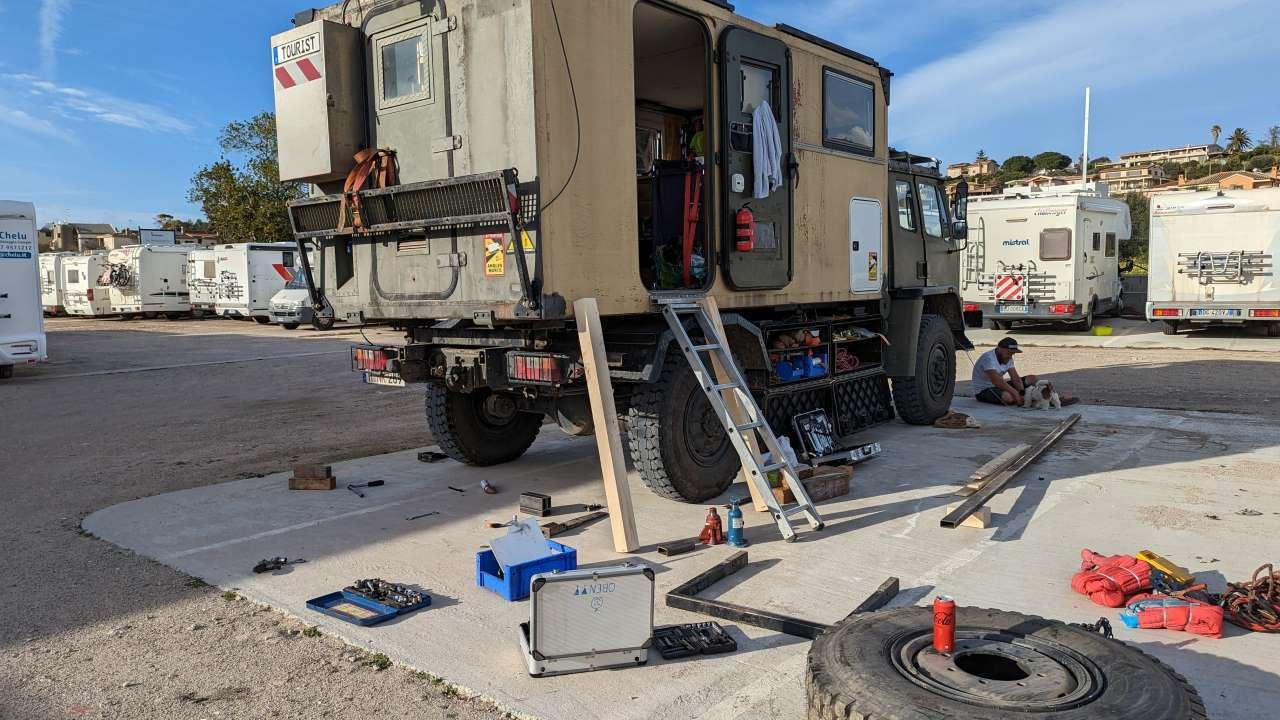
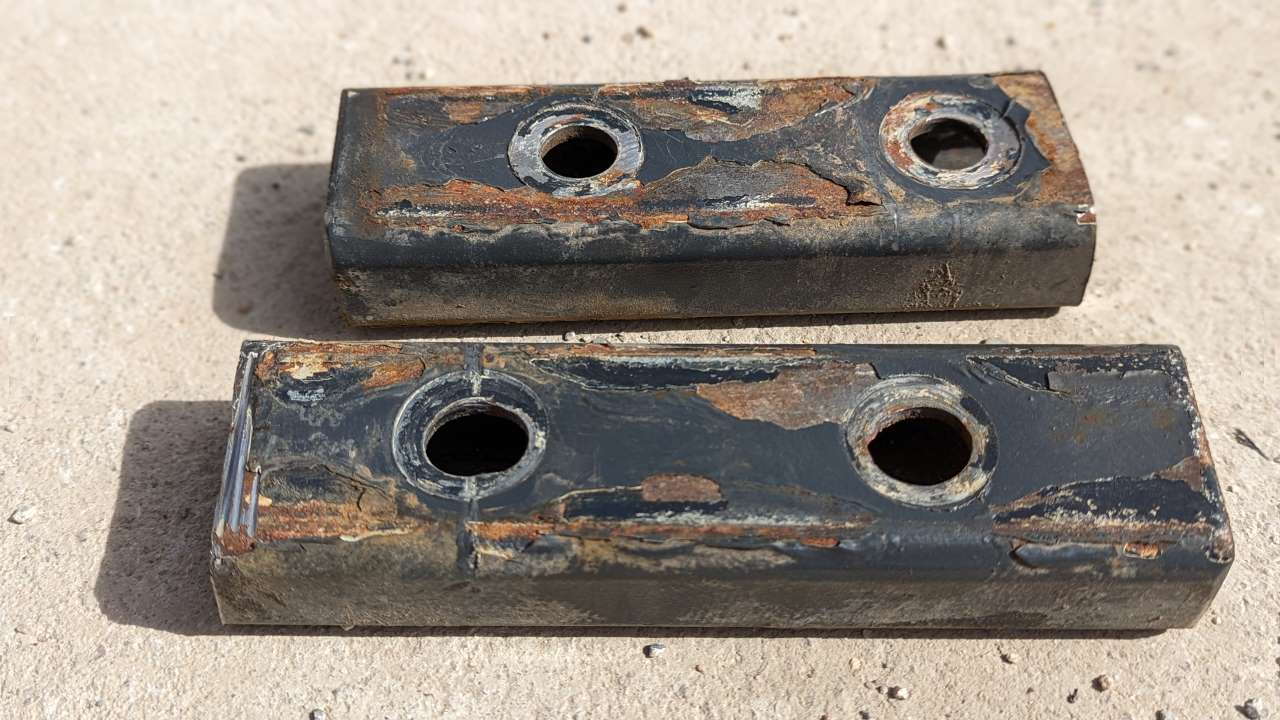


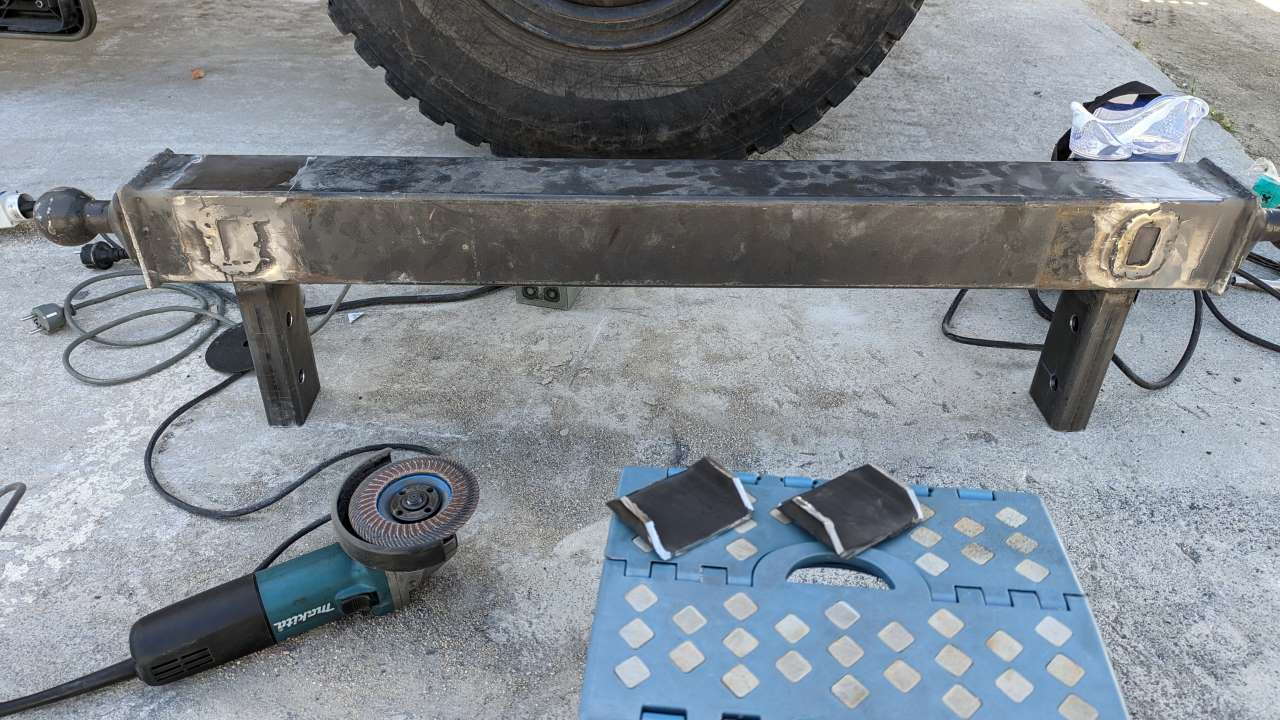
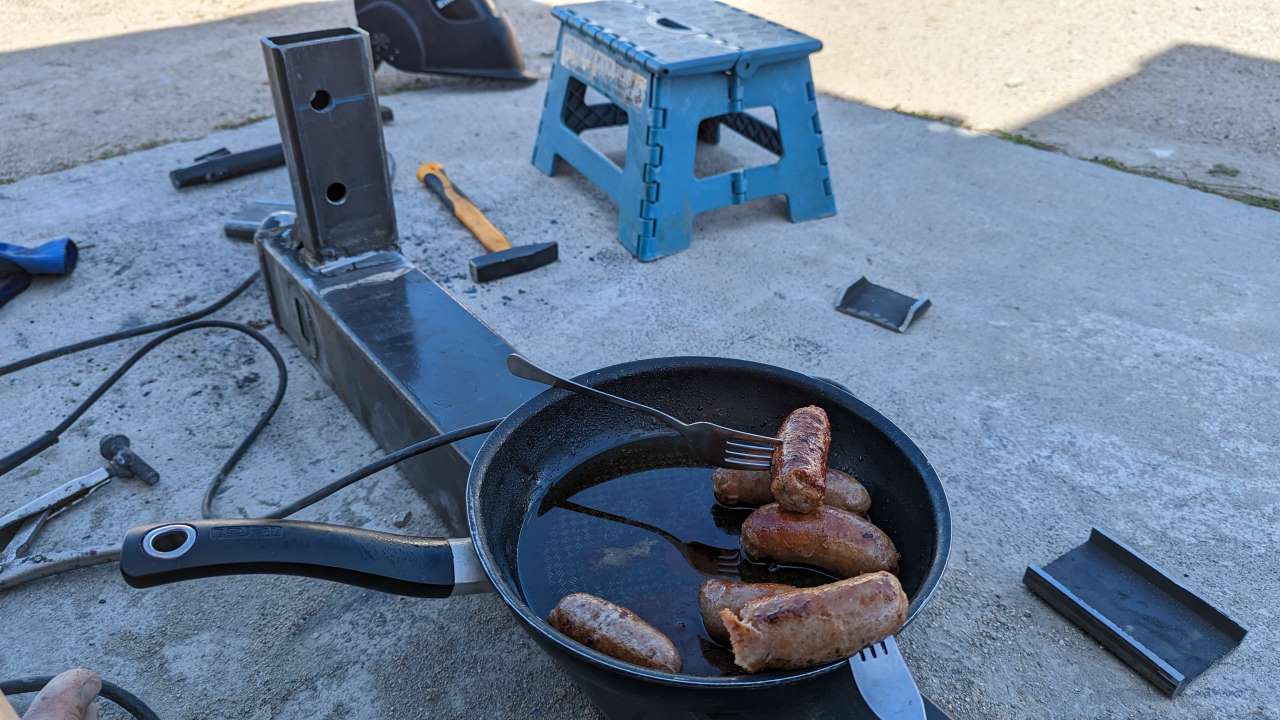
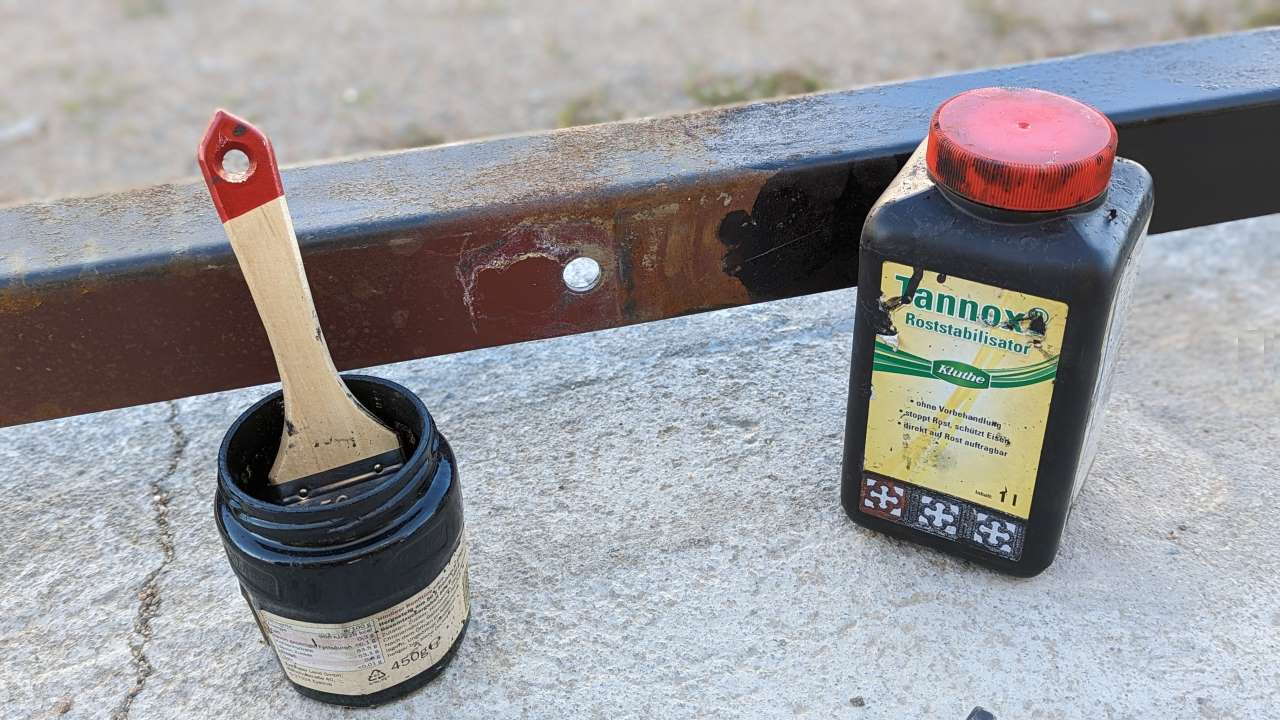
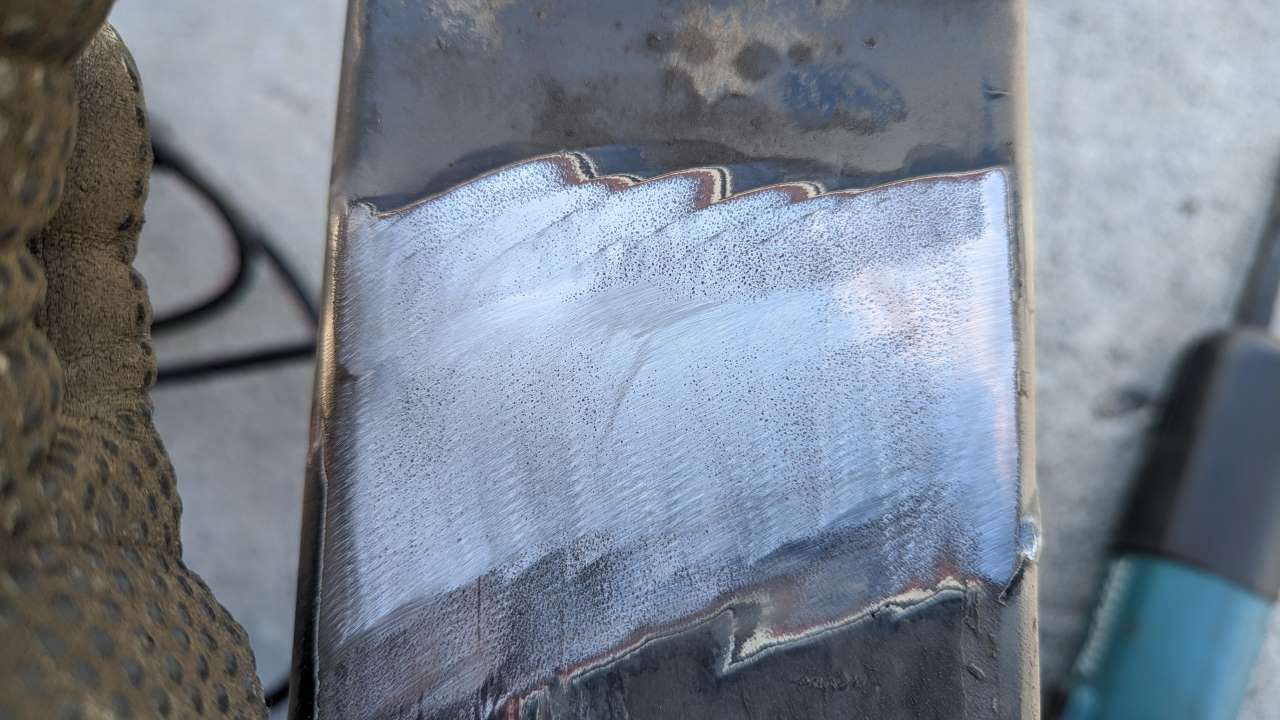
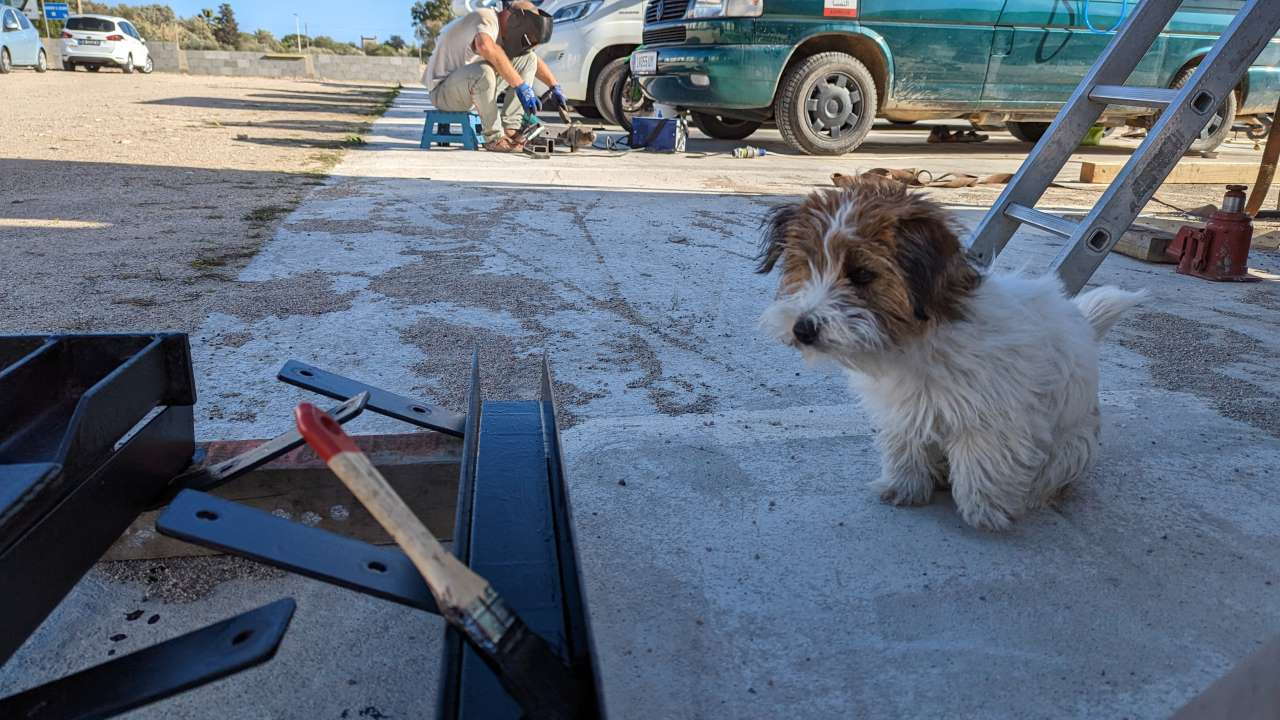
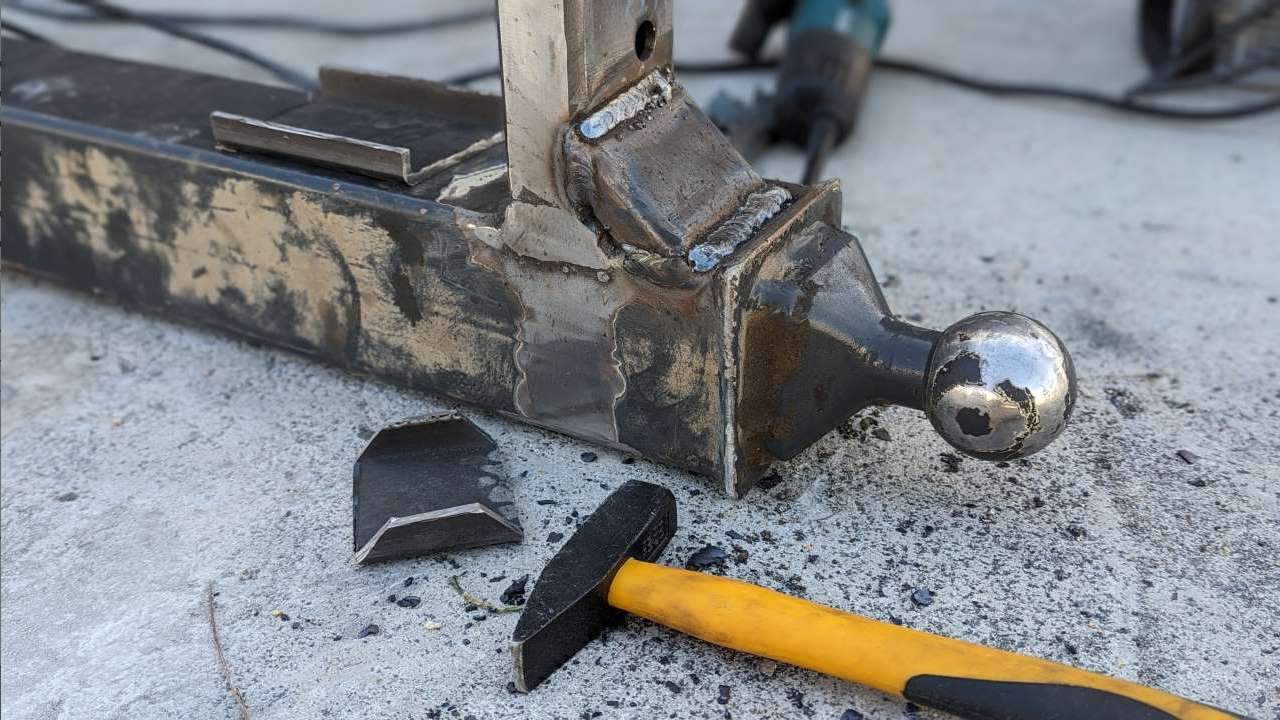
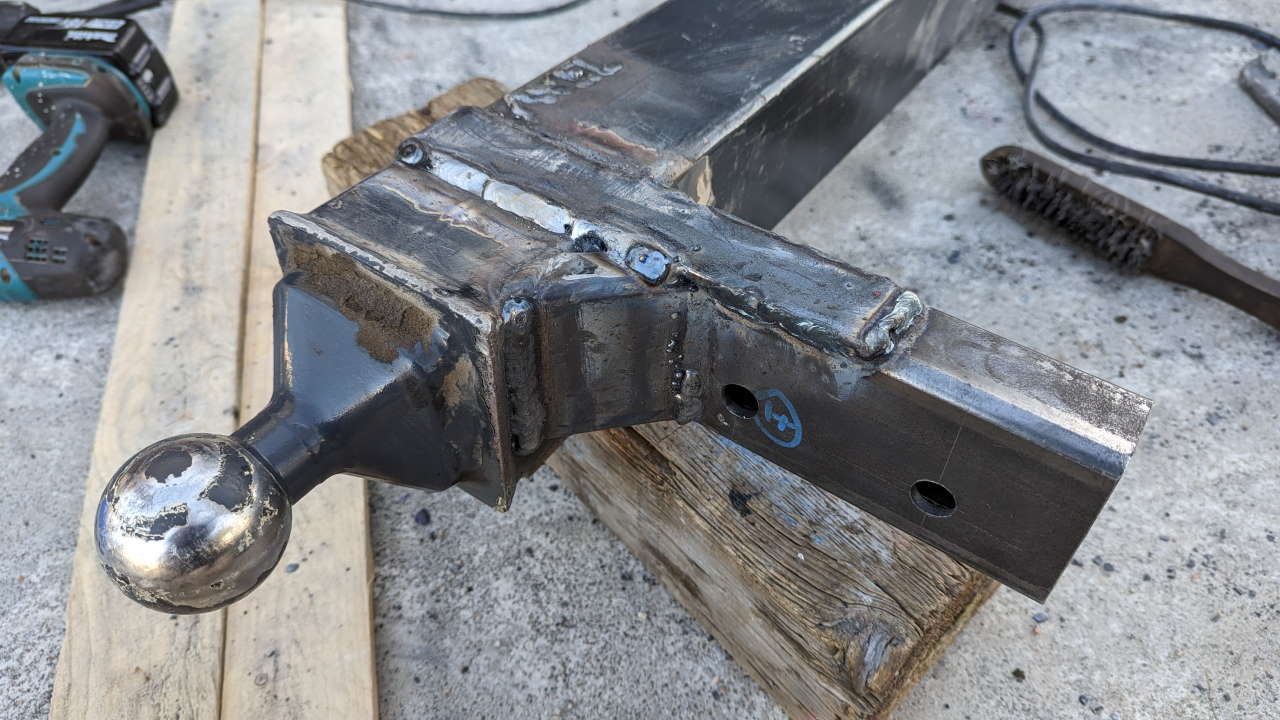
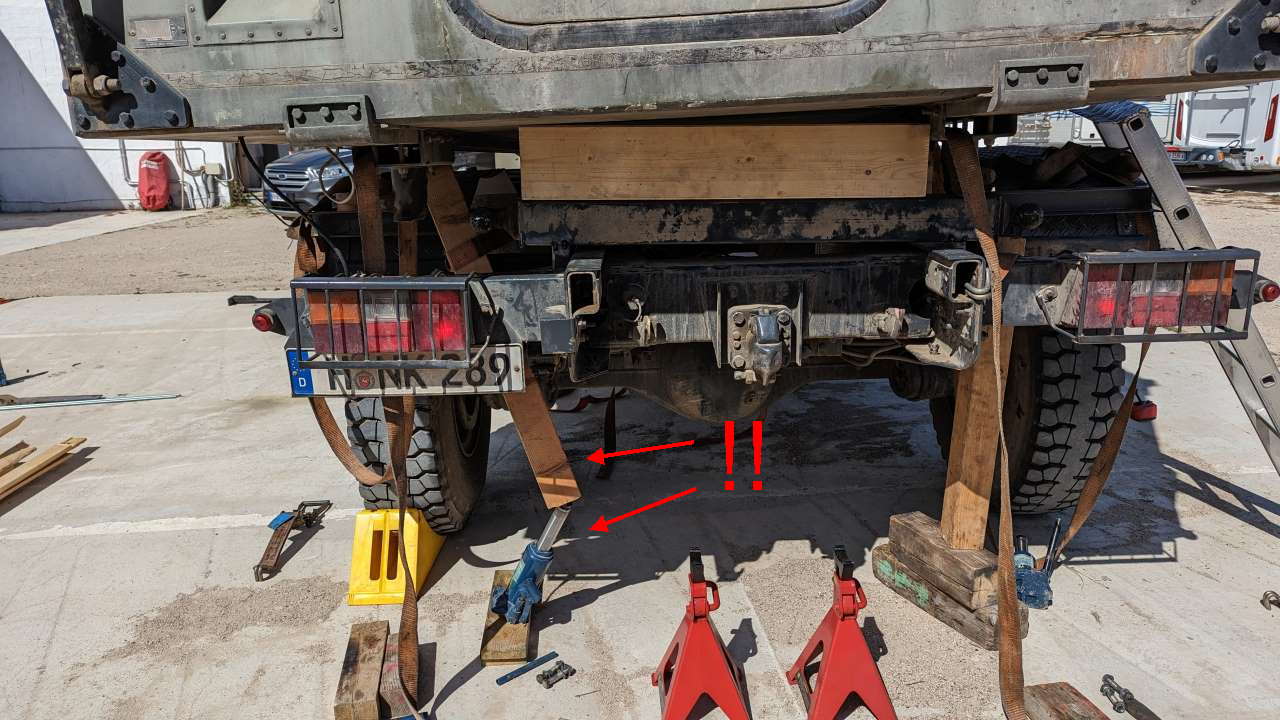
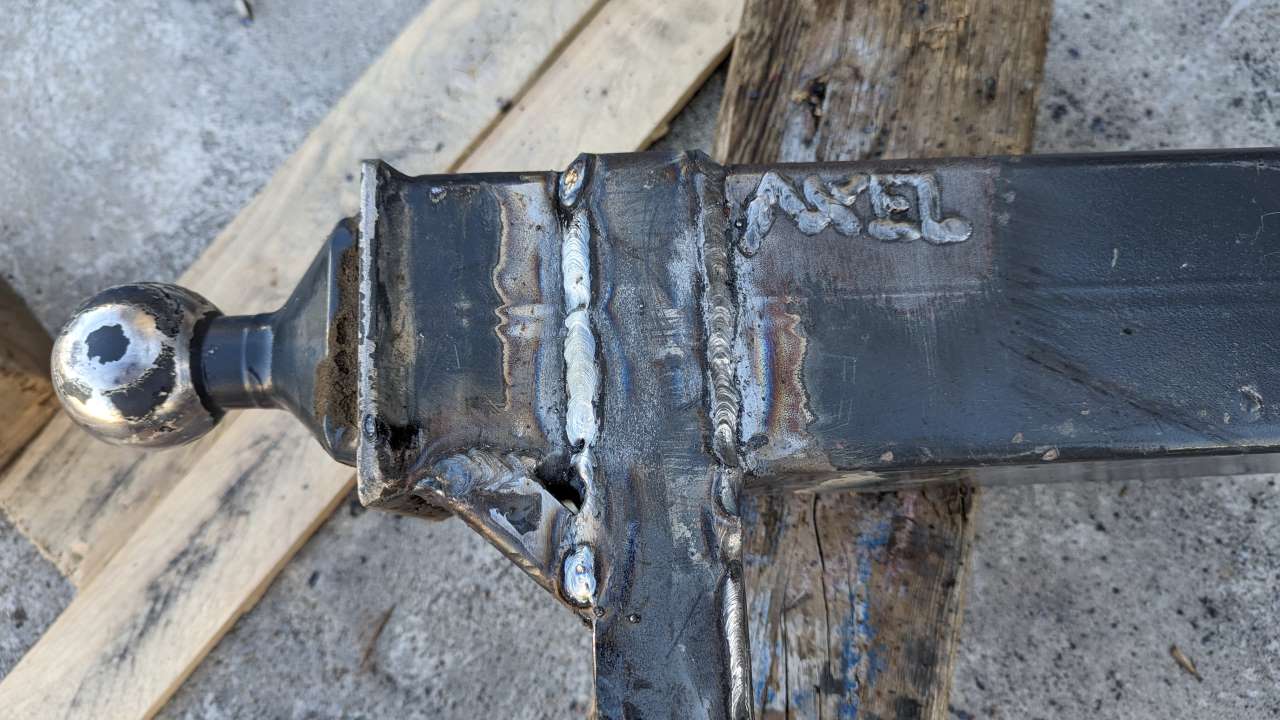
Es war nicht immer einfach mit uns beiden. Zwei Dickköpfe & Individualisten versuchen mit oft sehr unterschiedlichen Vorstellungen unter Feldbedingungen eine komplexe LKW Reparatur.
Keine Halle, kein Kran, keine Standbohrmaschine, nur ne Flex zum schneiden und nur mit dem Werkzeug, was an Board war. Wind und Staub und der Sonnenhitze ausgesetzt. Abenteuerlich.
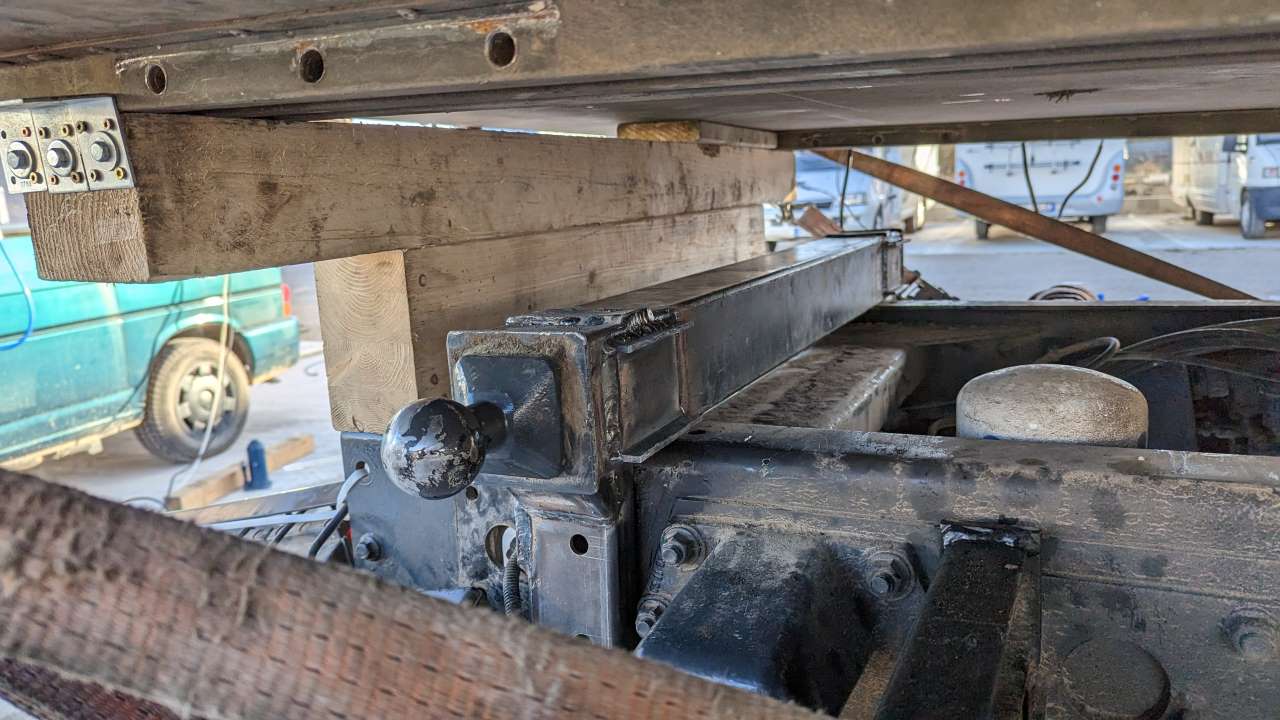
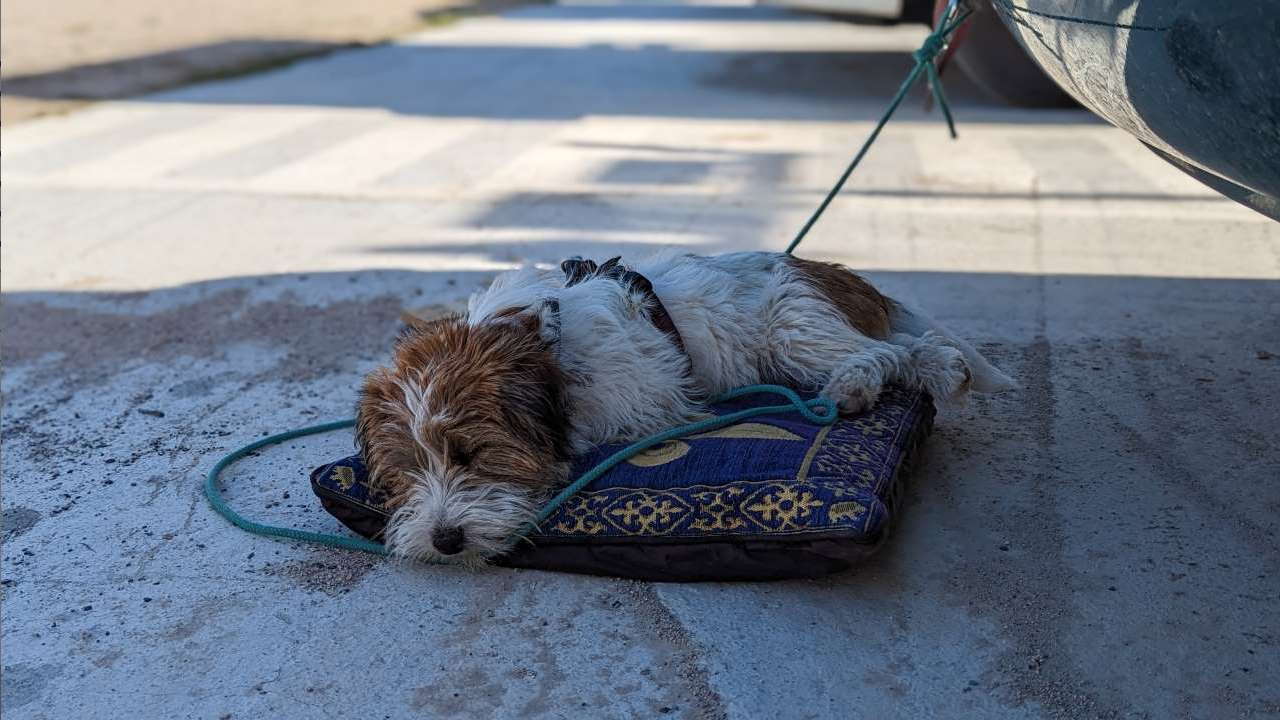
Ich hab inzwischen mit den Leuten aus Kirchheimbolanden telefoniert: keinerlei Einsicht. Und auch keine Reue, mich mit so einer lebensgefährlichen Konstruktion immer wieder auf die Piste zu schicken. Aber ich könnte vorbei kommen und dort den vierten Umbau / Verbesserung vornehmen lassen. Die ich selbstverständlich zu bezahlen hätte.
Die haben mir – allen ernstes – am Telefon ein weiteres Fangseil diesmal für hinten vorgeschlagen.
Kommen wir zu den bisherigen Kosten der Aktion in Sardinien:
Der Stellplatz hat inklusive Strom für vier Tage 120,- Euro gekostet. Die Kosten für benötigtes Werkzeug / gekaufte Ausrüstung waren etwa 150,- Euro. Die Rechnung bei Marini für die Stahlteile beliefen sich auf über 350,- Euro. Axel hat etwas für seine Reisekasse bekommen. Dazu kamen Sprit und die Einkäufe beim Holzhandel und weiterer kleinere Posten wie: benötigte Kleinteile & nochmal zum Baumarkt, McDonalds zum Tagesausklang.
Insgesamt sind damit (nachweislich) Kosten von knapp über 1000 Euro entstanden.
Zeitlicher Aufwand für die Reparatur unter schwierigen Bedingungen: kaum zu benennen. Axel hat einen eher fairen Preis für seine Reisekasse aufgerufen. Rund 1000 Euro Schaden / Arbeit für den von der Firma Fischer Fahrzeugbau Kirchheimbolanden erstellten, laienhaften Entwurf der Kippergelenkeaufhängung beim DAF T244 …
Anhang, Fotos der Original DAF T244 Befestigung der Pritsche (Bildrechte Thomas Wendel)
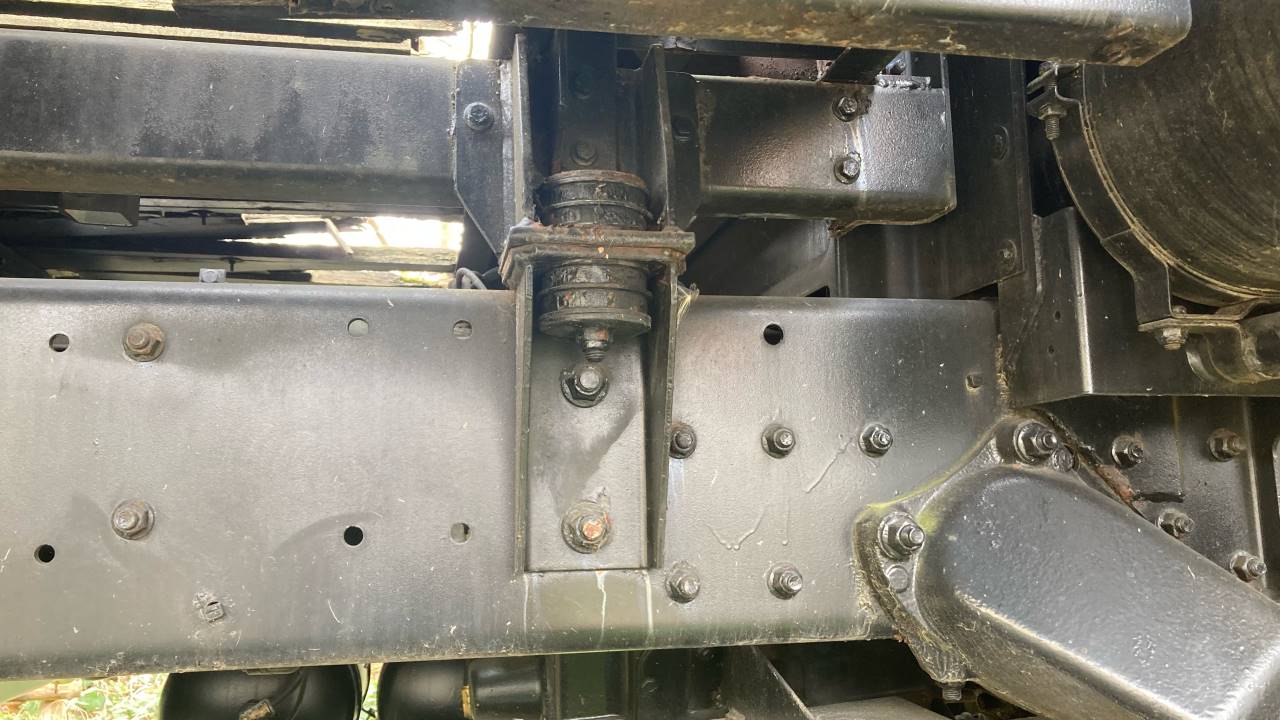
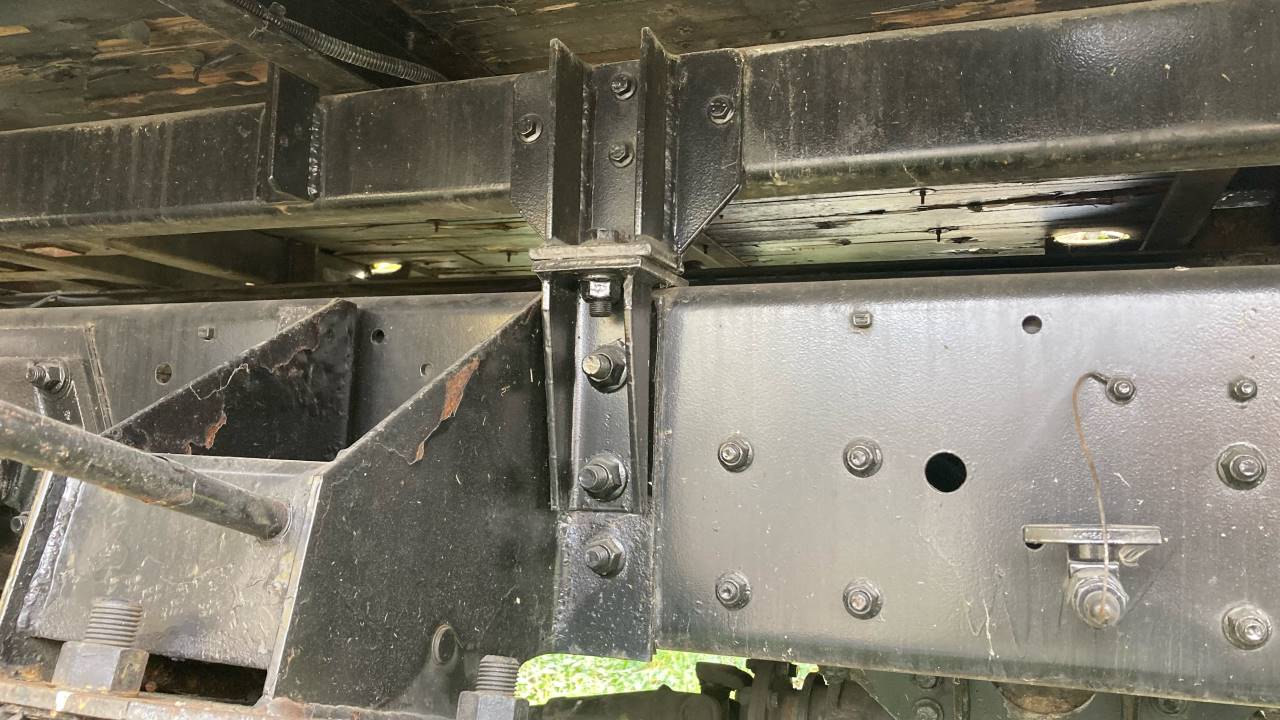
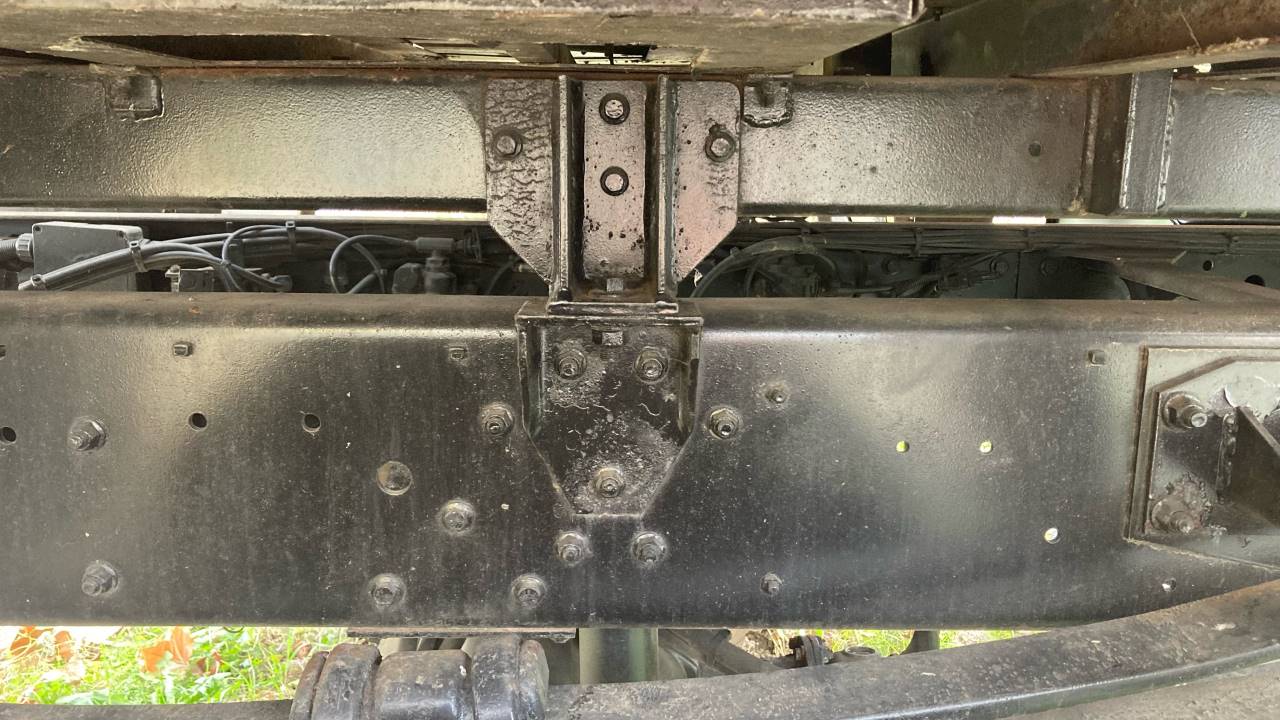
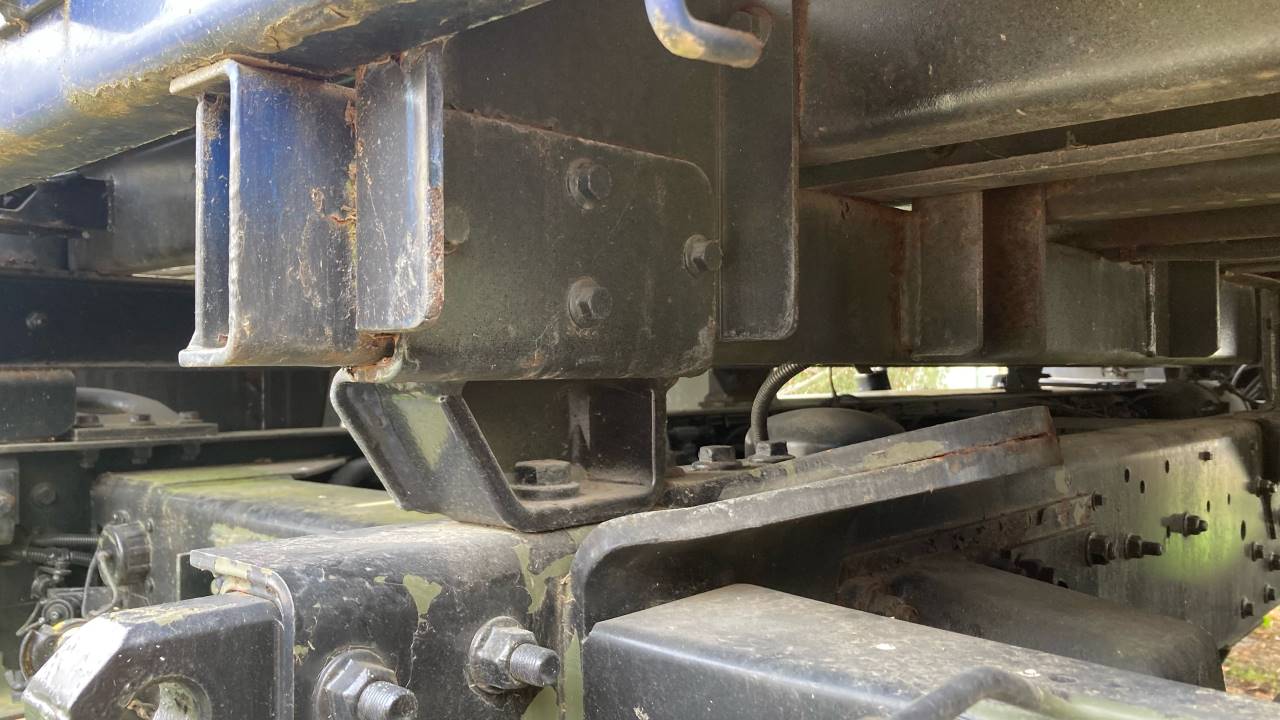
Danke an Thomas Wendel für das zuschicken und die Bildrechte !
Update, zwei Kabinenfotos
Inzwischen weiss ich mehr über meine Kabine. Bei mir ist das eine belgische Baeten Kabine. Diese ist im Gegensatz z.B. zu einem FM2 Shelter nicht eigenstabil und benötigt immer einen Zwischenrahmen.
Ohne Zwischenrahmen biegt die Kabine durch und bricht. Das ist bei mir leider der Fall. Eine Tatsache, welche Fahrzeugbau Fischer entweder nicht wusste oder es war ihnen egal. Ein professioneller Karoserie oder Fahrzeugbauer hat das im Kopf oder bringt es vor dem Umbau in Erfahrung.
Unfassbar, dieser Dilettantismus.
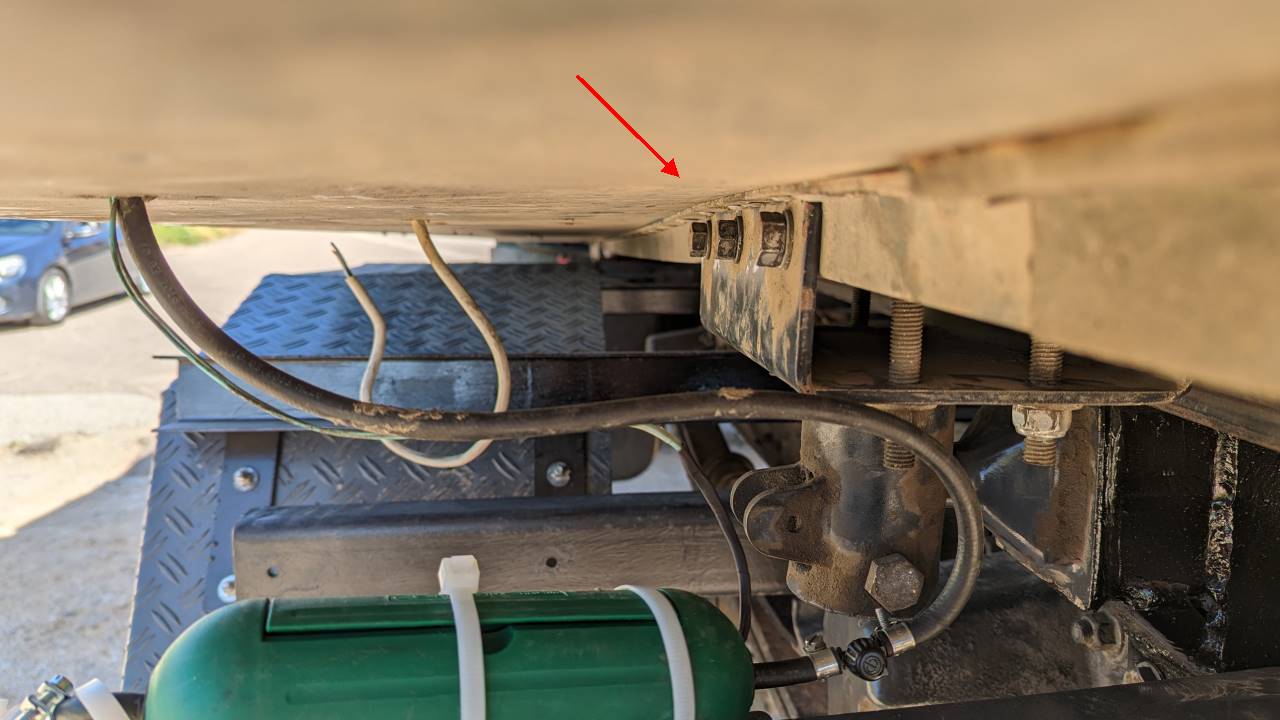
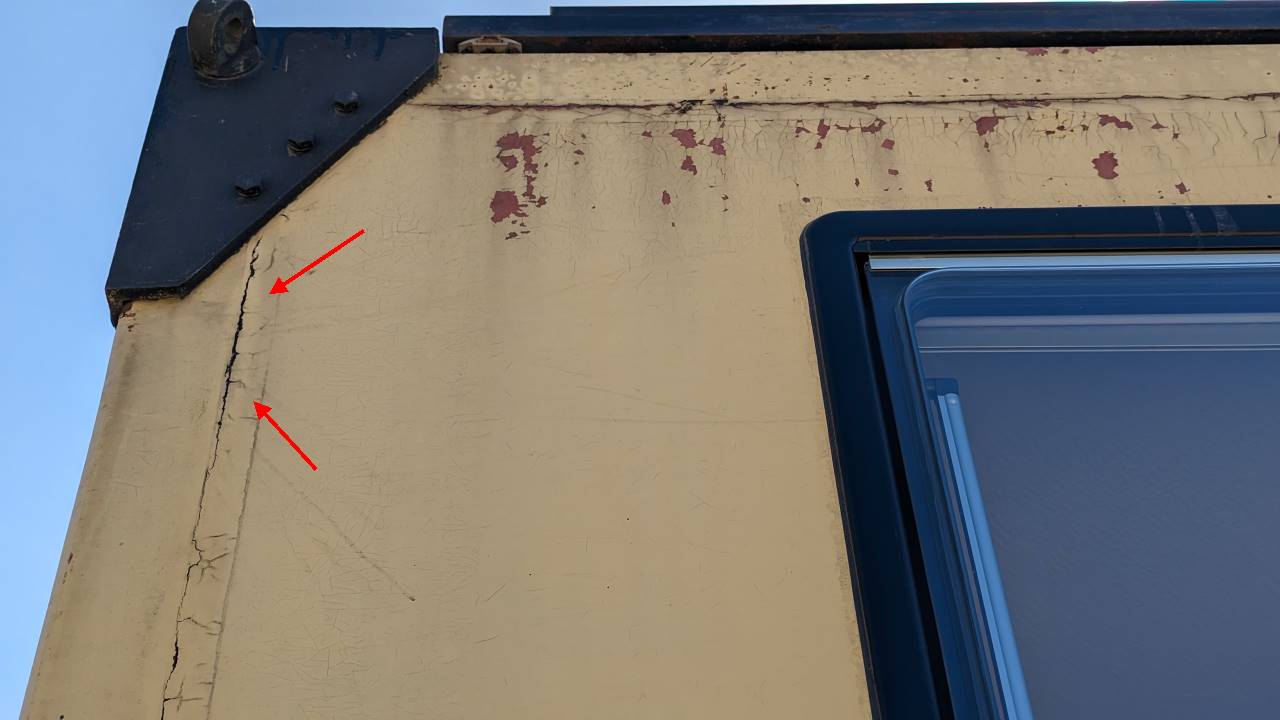
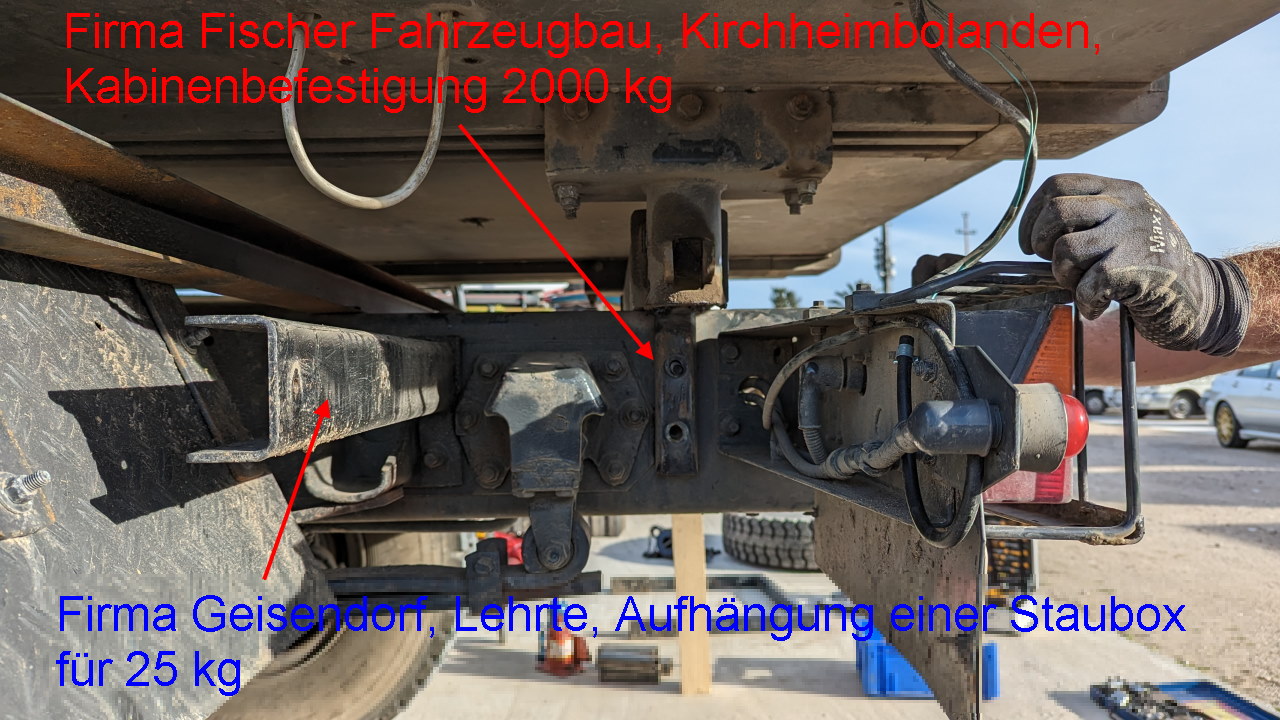
Fortsetzung folgt, vermutlich.
himmel hilf, was für eine aktion.
unter die kabine musst du noch rahmenzüge setzen, die wird dir irgendwann durchbrechen.
das gebastel mit den gewindestangen muss auch nochmal überarbeitet werden, da müssen rohrhülsen drüber, sonst zieht das garnicht, lockert sich.
insgesamt kein meisterwerk des fahrzeugbauers.
gruß, stefan
Zum Glück konnten wir die bisherigen 10.8 Schrauben weiter verwenden, um das Kippergelenk wieder festzuschrauben. Waren lang genug. Die Gewindestangen hab ich eher zur Sicherheit gekauft, da sie universell verwendbar sind. So wie es aussieht komme ich um einen Zwischenrahmen nicht herum.
Diese Firma hat falsch gemacht, was man falsch machen kann. Reparaturen können die glaube ich sogar ganz gut, aber den Aufbau von einem Expeditionsfahrzeug sollte man diesen Leuten auf gar keinen Fall anvertrauen. Völlig inkompetent, mit ihren „handwerklichen“ Lösungen.